A car coat rack structure
A coat rack and automobile technology, which is applied in the direction of rack configuration and the like, can solve the problem of uneven surface unevenness of the coat rack, and achieve the effects of improving the appearance quality, simplifying the production process and reducing the cost.
- Summary
- Abstract
- Description
- Claims
- Application Information
AI Technical Summary
Problems solved by technology
Method used
Image
Examples
Embodiment Construction
[0011] The present invention will be further described below in conjunction with the examples, but not as a limitation of the present invention.
[0012] See figure 1 , set the front and back sides of the corrugated cardboard 11 with glass fiber felt 12, evenly spray PU material on the front and back sides, put it into a mold to form a coat rack skeleton, and drill the blind holes 3 required for riveting plastic parts 2 on one side of the coat rack skeleton , the depth of the blind hole 3 does not exceed the thickness of the corrugated cardboard 11, and a layer of non-woven fabric layer 13 is bonded with hot-melt adhesive to improve the tactile feeling of the back of the part. The coat rack frame covered with non-woven fabric layer 13 is bonded with a layer of knitted fabric decorative layer 14 with hot melt adhesive on the front, and then the non-woven fabric layer 13 covering the blind hole 3 is ironed through to obtain the coat rack base material 1. Finally, the plastic pa...
PUM
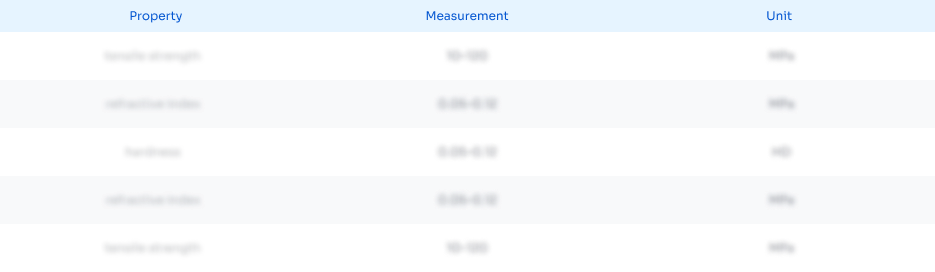
Abstract
Description
Claims
Application Information

- R&D
- Intellectual Property
- Life Sciences
- Materials
- Tech Scout
- Unparalleled Data Quality
- Higher Quality Content
- 60% Fewer Hallucinations
Browse by: Latest US Patents, China's latest patents, Technical Efficacy Thesaurus, Application Domain, Technology Topic, Popular Technical Reports.
© 2025 PatSnap. All rights reserved.Legal|Privacy policy|Modern Slavery Act Transparency Statement|Sitemap|About US| Contact US: help@patsnap.com