E glass fiber with low boron and low softening point, preparation method and application thereof
A low softening point and glass fiber technology, applied in the field of low boron and low softening point E glass fiber, can solve the problems of not being able to meet the performance requirements of yarn used in high-pressure oil pipelines, not being able to meet customers, and increasing raw material costs, etc., to achieve The effect of reducing energy consumption, reducing dependence, and reducing boron content
- Summary
- Abstract
- Description
- Claims
- Application Information
AI Technical Summary
Problems solved by technology
Method used
Image
Examples
preparation example Construction
[0025] The preparation method method of the low boron low softening point E glass fiber provided by the invention comprises the following steps:
[0026] a. Weighing, the raw materials used and their mass parts are: kaolin: 68-135; pyrophyllite: 285-460; quicklime: 150-200, dolomite: 65-95; Paoolite: 145~235; Fluorite: 13~28; Albite: 17~28, the sum of the ratio of each component is 1000; Albite, fluorite, dolomite, quicklime need to pass 100 mesh, silicon boron calcium Stone needs to pass 200 mesh, and kaolin, pyrophyllite and leucaosite need to pass 200-325 mesh;
[0027] b. Ingredients, start the agitator. After the agitator is running normally, pre-mix the fluorite and albite, and then send the pre-mixed raw materials together with the remaining raw materials in step a to the pneumatic mixing and agitating sender, and stir evenly. Degree greater than 92%;
[0028] c. Melting, send the homogeneously mixed materials in step b into a furnace to melt to obtain high-temperatur...
Embodiment 1
[0034] The amount of raw materials required is: Kaolin: 6.8kg, of which: SiO 2 ≥44.0%, Al 2 o 3 ≥37.5%, Fe 2 o 3 ≤0.6%, H 2 O≤1%; pyrophyllite: 45.0㎏, of which: SiO 2 ≥72%, Al 2 o 3 ≥16.5%, Fe 2 o 3 ≤0.45%, H 2 O≤1%; quicklime: 16.0㎏, of which: CaO≥85%, Fe 2 o 3 ≤0.15%, MgO≤3%, H 2 O≤1%; Dolomite: 7.0㎏, of which CaO≥30%, Fe 2 o 3 ≤0.15%, MgO≤21.0%, H 2 O ≤ 1%; Portlandite: 2.5㎏, its chemical composition is CaBSiO 4 (OH); leucoporite: 20.0㎏, of which SiO 2 ≥80.0%, Al 2 o 3 ≥10.0%, Fe 2 o 3 ≤0.50%, H 2 O≤1%; Fluorite: 2.0㎏, of which: CaF 2 ≥90%, H 2 O≤1%; albite: 1.7㎏, of which: SiO 2 ≥69.0%, Al 2 o 3 ≥17.0%, Fe 2 o 3 ≤0.35%, Na 2 O≥8.5%, H 2 O≤1%; the above percentages are mass percentages.
[0035] Before weighing, the composition content of CaO in quicklime should be detected every day, and the lime ratio should be adjusted according to the content of its composition.
[0036] The production steps are:
[0037]1. Take and weigh various raw mat...
Embodiment 2
[0051] The amount of raw materials required is: Kaolin: 9.2kg, of which: SiO 2 ≥44.0%, Al 2 o 3 ≥37.5%, Fe 2 o 3 ≤0.6%, H 2 O≤1%; pyrophyllite: 36.3㎏, of which: SiO 2 ≥72%, Al 2 o 3 ≥16.5%, Fe 2 o 3 ≤0.45%, H 2 O≤1%; quicklime: 16.5㎏, of which: CaO≥85%, Fe 2 o 3 ≤0.15%, MgO≤3%, H 2 O≤1%; dolomite: 8.3㎏, of which CaO≥30%, Fe 2 o 3 ≤0.15%, MgO≤21.0%, H 2 O ≤ 1%; Portlandite: 3.7㎏, its chemical composition is CaBSiO 4 (OH); leucoporite: 21.5㎏, of which SiO 2 ≥80.0%, Al 2 o 3 ≥10.0%, Fe 2 o 3 ≤0.50%, H 2 O≤1%; Fluorite: 2.2㎏, of which: CaF 2 ≥90%, H 2 O≤1%; albite: 2.3㎏, of which: SiO 2 ≥69.0%, Al 2 o 3 ≥17.0%, Fe 2 o 3 ≤0.35%, Na 2 O≥8.5%, H 2 O≤1%; the above percentages are mass percentages.
[0052] Before weighing, the composition content of CaO in quicklime should be detected every day, and the lime ratio should be adjusted according to the content of its composition.
[0053] The production steps are:
[0054] Before weighing, the composition...
PUM
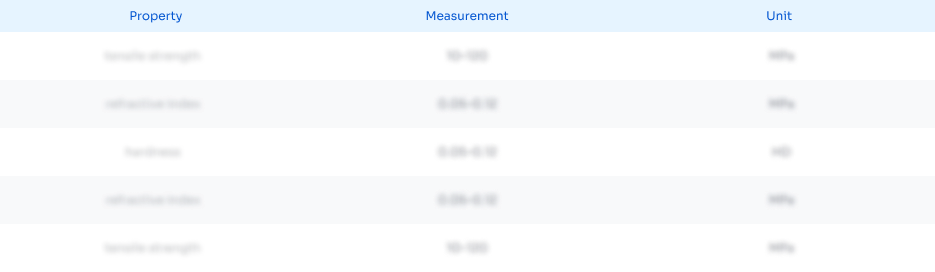
Abstract
Description
Claims
Application Information

- R&D
- Intellectual Property
- Life Sciences
- Materials
- Tech Scout
- Unparalleled Data Quality
- Higher Quality Content
- 60% Fewer Hallucinations
Browse by: Latest US Patents, China's latest patents, Technical Efficacy Thesaurus, Application Domain, Technology Topic, Popular Technical Reports.
© 2025 PatSnap. All rights reserved.Legal|Privacy policy|Modern Slavery Act Transparency Statement|Sitemap|About US| Contact US: help@patsnap.com