Method for determining reduction factor of bearing capacity of axial load cylindrical shell structure
A determination method and technology of bearing capacity, applied in the field of determination of bearing capacity reduction factor of axial compression shell structure, can solve the problems of lack of clarity and adequacy, and high experimental cost.
- Summary
- Abstract
- Description
- Claims
- Application Information
AI Technical Summary
Problems solved by technology
Method used
Image
Examples
Embodiment 1
[0071] refer to Figure 4 with Figure 5 , the radius of the metal cylindrical shell R = 250 mm, length L = 510 mm, thickness t = 0.5 mm. The material is 2024 aluminum alloy: modulus of elasticity E = 72 GPa, Poisson's ratio υ = 0.31, yield stress σ s = 363 MPa, ultimate stress σ b = 463 MPa, density ρ = 2.8E-6 kg / mm 3 . In order to facilitate clamping and loading, T-rings are arranged at the bottom and top of the cylindrical shell, and the material is the same as that of the cylindrical shell. The bottom end of the T-ring is fixed, and the top end is fully restrained except for the axial translational displacement.
[0072] refer to Figure 6 , the radial concentrated force is applied to introduce the initial defect along the five equal parts of the axial direction, and the curves of the radial concentrated force and the buckling load value of the structure are drawn. Assuming that there is an initial defect (1.5mm) that is 3 times the thickness of th...
Embodiment 2
[0076] refer to Figure 11 with Figure 12 , the radius of the composite cylindrical shell R = 250 mm, length L = 510 mm. The layering of the cylindrical shell is [45 / -45 / 45 / -45 / 45], the thickness of the single layer is 0.1mm, and the material constant is: E 11 = 84.56 GPa, E 22 = 6.86 GPa, G 12 = G 13 = 4.9 GPa, G 23 = 1.96 GPa, υ 12 = 0.3, ρ = 1.7E-6 kg / mm 3 . In order to facilitate clamping and loading, T-rings are set at the bottom and top of the cylindrical shell, using 2024 aluminum alloy: modulus of elasticity E = 72 GPa, Poisson's ratio υ = 0.31, yield stress σ s = 363 MPa, ultimate stress σ b = 463 MPa, density ρ = 2.8E-6 kg / mm 3 . The bottom end of the T-ring is fixed, and the top end is fully restrained except for the axial translational displacement.
[0077] refer to Figure 13 , respectively apply radial concentrated force to introduce initial defects along the five equal parts of the axial direction, and draw the cu...
Embodiment 3
[0081] refer to Figure 18 with Figure 19 , the radius of the metal cylindrical shell R = 300 mm, length L = 600 mm, thickness t = 0.5 mm. The material is 2024 aluminum alloy: modulus of elasticity E = 72 GPa, Poisson's ratio υ = 0.31, yield stress σ s = 363 MPa, ultimate stress σ b = 463 MPa, density ρ = 2.8E-6 kg / mm 3 . In order to facilitate clamping and loading, T-rings are arranged at the bottom and top of the cylindrical shell, and the material is the same as that of the cylindrical shell. The bottom end of the T-ring is fixed, and the top end is fully restrained except for the axial translational displacement.
[0082] refer to Figure 20 , respectively apply radial concentrated force to introduce the initial defect along the six equal parts of the axial direction, and draw the curve of radial concentrated force and structural buckling load value Figure 21 . Assuming that there is an initial defect (1.5mm) that is three times the thickness ...
PUM
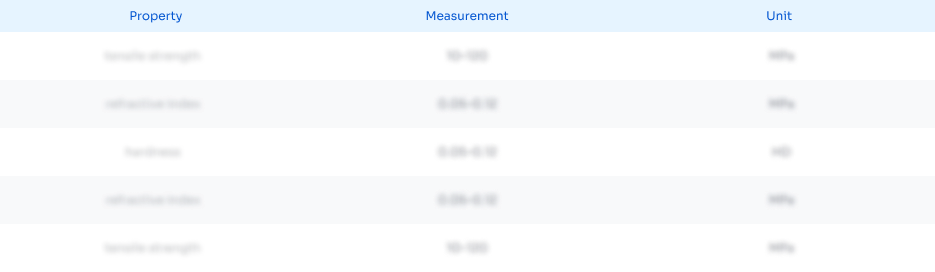
Abstract
Description
Claims
Application Information

- R&D
- Intellectual Property
- Life Sciences
- Materials
- Tech Scout
- Unparalleled Data Quality
- Higher Quality Content
- 60% Fewer Hallucinations
Browse by: Latest US Patents, China's latest patents, Technical Efficacy Thesaurus, Application Domain, Technology Topic, Popular Technical Reports.
© 2025 PatSnap. All rights reserved.Legal|Privacy policy|Modern Slavery Act Transparency Statement|Sitemap|About US| Contact US: help@patsnap.com