Attitude measurement method of micro-electro mechanical system (MEMS) inertial navigation system based on single-shaft forward revolution and reverse revolution
An inertial navigation system and measurement method technology, applied in the field of measurement, can solve the problems of constant value deviation of inertial devices, difficulty in improving attitude accuracy of inertial navigation system, etc.
- Summary
- Abstract
- Description
- Claims
- Application Information
AI Technical Summary
Problems solved by technology
Method used
Image
Examples
Embodiment Construction
[0046] The specific embodiment of the present invention is described in detail below in conjunction with accompanying drawing:
[0047] (1) Use the global positioning system to determine the initial position parameters of the carrier, and bind them to the navigation computer;
[0048] (2) After the MEMS inertial navigation system is preheated, the output data of the MEMS gyroscope and the MEMS accelerometer are collected;
[0049] (3) Determine the angle information between the IMU coordinate system and the navigation coordinate system according to the relationship between the carrier motion acceleration information measured by the MEMS accelerometer and the local gravitational acceleration and the relationship between the carrier angular velocity information output by the MEMS gyroscope and the earth's rotation angular rate, and complete The initial alignment process of the system, the establishment of the initial strapdown matrix of the MEMS inertial navigation system
[...
PUM
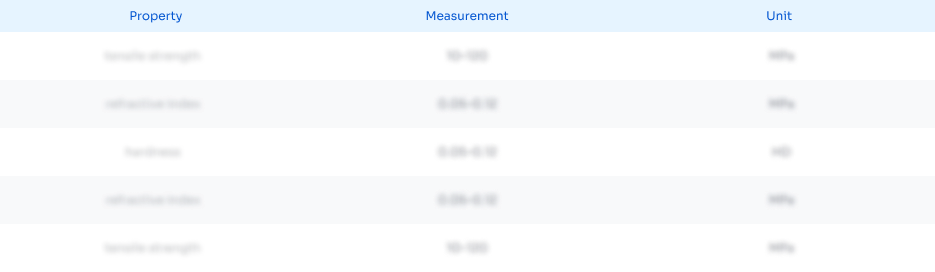
Abstract
Description
Claims
Application Information

- Generate Ideas
- Intellectual Property
- Life Sciences
- Materials
- Tech Scout
- Unparalleled Data Quality
- Higher Quality Content
- 60% Fewer Hallucinations
Browse by: Latest US Patents, China's latest patents, Technical Efficacy Thesaurus, Application Domain, Technology Topic, Popular Technical Reports.
© 2025 PatSnap. All rights reserved.Legal|Privacy policy|Modern Slavery Act Transparency Statement|Sitemap|About US| Contact US: help@patsnap.com