Horizontal bending machine
A technology of bending machine and bending mechanism, which is applied in the field of bending machines, can solve the problems of difficulty in putting in and taking out workpieces, failure to automate, and affecting bending efficiency, so as to improve product quality and stability, and facilitate multiple Secondary bending, the effect of improving the quality of the workpiece
- Summary
- Abstract
- Description
- Claims
- Application Information
AI Technical Summary
Problems solved by technology
Method used
Image
Examples
Embodiment Construction
[0059] The present invention will be further described in detail below in conjunction with the accompanying drawings and embodiments.
[0060] Such as figure 1 As shown, the horizontal bending machine includes a body 1, a controller 8, a bending die 3 and its first driving mechanism 301, a second driving mechanism 302, a binder 2 and its moving mechanism 201 for the binder, and a follower Plate 4, a workbench 6 arranged above the fuselage, a conveying device 5 and a feeding device 7 installed on the workbench 6.
[0061] Such as Figure 11 , Figure 5 As shown, the bending mechanism includes a binder plate 2, a binder plate rotating member, a binder plate rotating mechanism 301 that drives the binder plate rotating member to rotate, a bending die device 3, and a bending die rotating mechanism 302 that drives the bending die device to rotate, The binder plate 2 is connected on the binder plate rotating part, the rotating shaft 308 of the bending die is connected to the press...
PUM
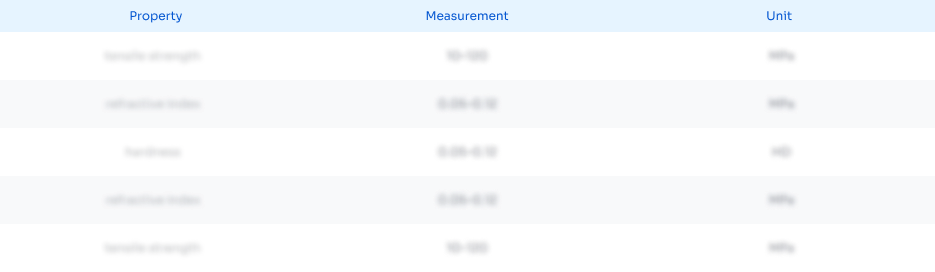
Abstract
Description
Claims
Application Information

- Generate Ideas
- Intellectual Property
- Life Sciences
- Materials
- Tech Scout
- Unparalleled Data Quality
- Higher Quality Content
- 60% Fewer Hallucinations
Browse by: Latest US Patents, China's latest patents, Technical Efficacy Thesaurus, Application Domain, Technology Topic, Popular Technical Reports.
© 2025 PatSnap. All rights reserved.Legal|Privacy policy|Modern Slavery Act Transparency Statement|Sitemap|About US| Contact US: help@patsnap.com