Optimization process of vacuum potassium carbonate method coke oven gas desulfurization and equipment thereof
A technology of vacuum potassium carbonate and coke oven gas, which is applied in the fields of combustible gas purification, combustible gas purification/transformation, and petroleum industry, etc., can solve the problems of reduced microbial activity in biochemical systems, large consumption of NaOH lye, and high alkali consumption in gas purification. Achieve the effect of minimizing production, saving pharmaceutical costs, and improving yield
- Summary
- Abstract
- Description
- Claims
- Application Information
AI Technical Summary
Problems solved by technology
Method used
Image
Examples
Embodiment Construction
[0030] The present invention will be further described below in conjunction with the accompanying drawings and specific embodiments, but the present invention is not limited to the following embodiments.
[0031] figure 1 The vacuum potassium carbonate method coke oven gas desulfurization equipment shown in , includes a desulfurization tower 1 for absorbing acid gas in coke oven gas and a regeneration tower 2 for regenerating the desulfurization rich liquid, the desulfurization tower at the bottom of the lower section of the desulfurization tower 1 The rich liquid outlet 3 is connected to the input end of the rich liquid tank 4, and the top of the rich liquid tank 4 is provided with a potassium salt replenishment port 12, and the output end of the rich liquid tank 4 passes through the heat medium pipeline of the heat exchanger 15 and the regeneration The rich liquid inlet 5 at the top of the tower 2 is connected, the lean liquid outlet 6 at the bottom of the regeneration tower...
PUM
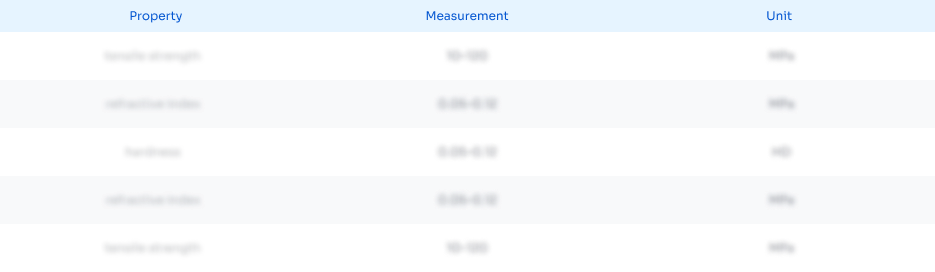
Abstract
Description
Claims
Application Information

- Generate Ideas
- Intellectual Property
- Life Sciences
- Materials
- Tech Scout
- Unparalleled Data Quality
- Higher Quality Content
- 60% Fewer Hallucinations
Browse by: Latest US Patents, China's latest patents, Technical Efficacy Thesaurus, Application Domain, Technology Topic, Popular Technical Reports.
© 2025 PatSnap. All rights reserved.Legal|Privacy policy|Modern Slavery Act Transparency Statement|Sitemap|About US| Contact US: help@patsnap.com