Self-adaption electronic differential control system
An electronic differential control and self-adaptive technology, applied in the control drive, electric vehicle, power management and other directions, can solve the problems of weak self-adaptation, delay effect, poor dynamic performance, etc., to achieve smooth operation, smooth steering, and cost savings.
- Summary
- Abstract
- Description
- Claims
- Application Information
AI Technical Summary
Problems solved by technology
Method used
Image
Examples
Embodiment Construction
[0030] In order to make the object, technical solution and advantages of the present invention clearer, the present invention will be further described in detail below in conjunction with the accompanying drawings and embodiments. It should be understood that the specific embodiments described here are only used to explain the present invention, not to limit the present invention.
[0031] Such as figure 1 As shown, the self-adaptive electronic differential speed control method of the embodiment of the present invention is used for the driving control of the automobile, comprising the following steps:
[0032] S101. Obtain the motor speeds of the two driving wheels and the running speed of the vehicle;
[0033] S102, according to the slip ratio of the two drive wheels according to the motor speed and the running speed of the vehicle;
[0034] S103, judging whether the difference in slip ratio is greater than a preset value;
[0035] S104. If the difference between the slip ...
PUM
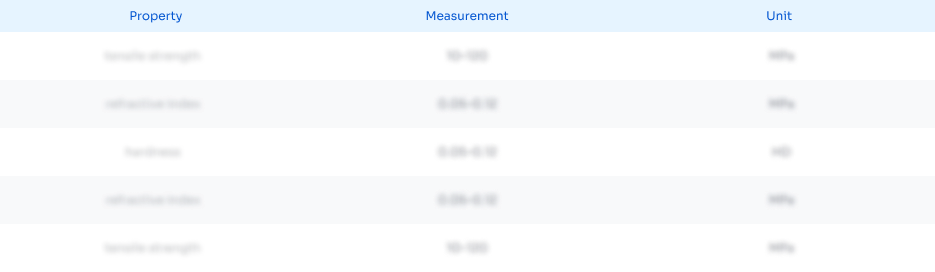
Abstract
Description
Claims
Application Information

- R&D
- Intellectual Property
- Life Sciences
- Materials
- Tech Scout
- Unparalleled Data Quality
- Higher Quality Content
- 60% Fewer Hallucinations
Browse by: Latest US Patents, China's latest patents, Technical Efficacy Thesaurus, Application Domain, Technology Topic, Popular Technical Reports.
© 2025 PatSnap. All rights reserved.Legal|Privacy policy|Modern Slavery Act Transparency Statement|Sitemap|About US| Contact US: help@patsnap.com