Signal wireless electromagnetism transmission system while drilling
A radio and magnetic transmission technology, applied in the field of transmission while drilling, can solve the problems of destroying the drill pipe structure, redesigning the drill pipe, and greatly affecting the transmission performance, so as to increase the transmission distance, improve the directivity and gain, and transmit fast effect
- Summary
- Abstract
- Description
- Claims
- Application Information
AI Technical Summary
Problems solved by technology
Method used
Image
Examples
Embodiment Construction
[0020] The wireless electromagnetic transmission system of the signal while drilling according to the present invention, such as figure 1 As shown, the transmission system is arranged on the drilling well, and the drilling includes a drill pipe 11, a drilling tool 12, and a drill collar 13. The two sections of drill pipe 11 can be directly connected, and can be connected by a metal drill pipe short 15. The drill pipe 11 and the drilling tool 12 are connected by drill collar 13. The transmission system includes a drill pipe 11 , a drill collar 13 , a drill tool 12 , an electromagnetic signal transmitting module 21 , a relay shorting module 23 , and an electromagnetic signal receiving module 22 .
[0021] The receiving module 22 comprises an annular metal pipe 14 . The annular metal pipe 14 is sheathed on the drill pipe 11 exposed to the ground, and the inner diameter of the annular metal pipe 14 is larger than the outer diameter of the drill pipe 11 . The transmitting module ...
PUM
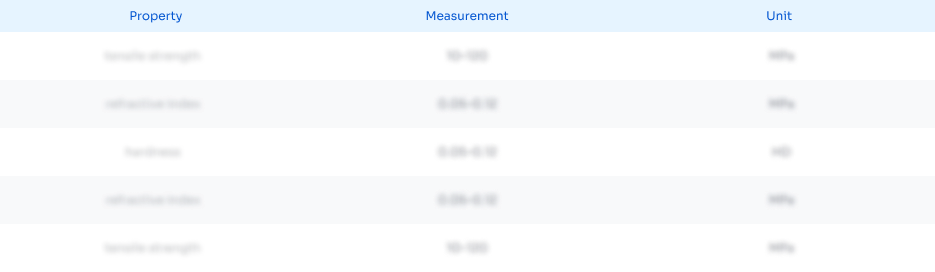
Abstract
Description
Claims
Application Information

- R&D
- Intellectual Property
- Life Sciences
- Materials
- Tech Scout
- Unparalleled Data Quality
- Higher Quality Content
- 60% Fewer Hallucinations
Browse by: Latest US Patents, China's latest patents, Technical Efficacy Thesaurus, Application Domain, Technology Topic, Popular Technical Reports.
© 2025 PatSnap. All rights reserved.Legal|Privacy policy|Modern Slavery Act Transparency Statement|Sitemap|About US| Contact US: help@patsnap.com