Turbine Rotor Vehicle Fixture
A technology for turbine rotors and vehicles, which is applied in clamping, manufacturing tools, supports, etc., and can solve problems that affect the quality of center hole processing
- Summary
- Abstract
- Description
- Claims
- Application Information
AI Technical Summary
Problems solved by technology
Method used
Image
Examples
Embodiment Construction
[0016] See Figure 1 to Figure 5 , a fixture for a turbine rotor vehicle, which includes a chassis 12 and a counterweight 1, the counterweight 1 is mounted on the edge of the chassis 12 through bolts, and includes a positioning device, the positioning device includes a positioning sleeve 6 and a centering nut 11, and the centering nut 11 Vertically installed in the center of the chassis 12 and fastened with bolts, the top of the centering nut 11 is provided with a positioning ring, the positioning sleeve 6 is installed on the outside of the centering nut 11, and is threaded with it, and one end of the positioning sleeve 6 is rigidly connected with a balance plate 17, to be processed The turbine rotor 16 is installed in the positioning sleeve 6, its shorter shaft end is fixed in the centering nut positioning ring 21, and its long shaft end is pressed by the balance plate 17; it also includes a clamping device, and the two sides of the positioning device are clamped The device i...
PUM
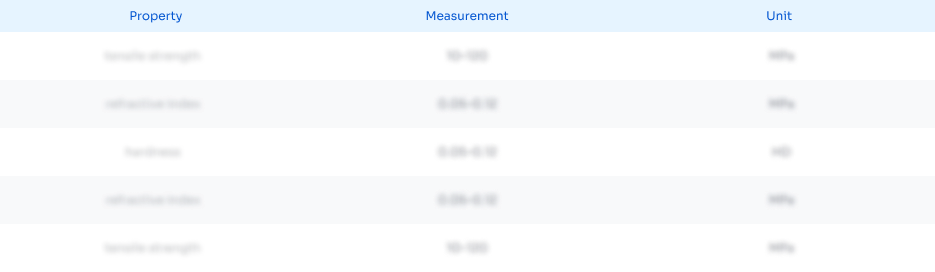
Abstract
Description
Claims
Application Information

- R&D
- Intellectual Property
- Life Sciences
- Materials
- Tech Scout
- Unparalleled Data Quality
- Higher Quality Content
- 60% Fewer Hallucinations
Browse by: Latest US Patents, China's latest patents, Technical Efficacy Thesaurus, Application Domain, Technology Topic, Popular Technical Reports.
© 2025 PatSnap. All rights reserved.Legal|Privacy policy|Modern Slavery Act Transparency Statement|Sitemap|About US| Contact US: help@patsnap.com