Connection structure of intelligent power module terminal
A technology of intelligent power modules and connection structures, applied in the direction of output power conversion devices, electrical components, etc., can solve the problems of long process time, high bending process requirements, and low welding performance, so as to improve the firmness and reliability , Solve the effects of excessive contact resistance, good size and flatness
- Summary
- Abstract
- Description
- Claims
- Application Information
AI Technical Summary
Problems solved by technology
Method used
Image
Examples
Embodiment Construction
[0015] See figure 1 As shown, in the smart power module terminal of the present invention, the terminal 1 has a stepped structure, and the terminal 1 includes a vertical connecting column 1-1, an upper bonding seat 1-2 arranged at the lower part of the connecting column 1-1, and a lower The bonding seat 1-4 and the connecting seat 1-3 vertically placed between the upper bonding seat 1-2 and the lower bonding seat 1-4, its connecting column 1-1, the upper bonding seat 1-2, the connection Both the seat 1-3 and the lower bonding seat 1-4 are fixed with the shell 2. See figure 1 As shown in , the connecting column 1-1 of the terminal 1 of the present invention is in an inverted T shape. The terminal 1 of the present invention is an electrode terminal or / and a signal terminal.
[0016] See Figure 1-5 As shown, in the connection structure of the intelligent power module terminal of the present invention, the terminal 1 is embedded in the periphery of the window of the shell 2, ...
PUM
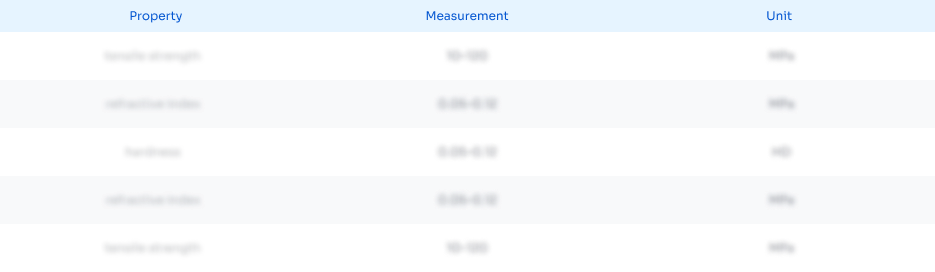
Abstract
Description
Claims
Application Information

- Generate Ideas
- Intellectual Property
- Life Sciences
- Materials
- Tech Scout
- Unparalleled Data Quality
- Higher Quality Content
- 60% Fewer Hallucinations
Browse by: Latest US Patents, China's latest patents, Technical Efficacy Thesaurus, Application Domain, Technology Topic, Popular Technical Reports.
© 2025 PatSnap. All rights reserved.Legal|Privacy policy|Modern Slavery Act Transparency Statement|Sitemap|About US| Contact US: help@patsnap.com