Catalytic cracking and catalytic gasoline hydrogenation combined process
A catalytic gasoline and catalytic cracking technology, which is applied in the fields of hydrotreating process, petroleum industry, and hydrocarbon oil treatment, can solve the problems of poor adaptability of raw materials and different technological processes, so as to reduce energy consumption, mature and reliable technical solutions, and reduce The effect of plant modification investment and operating costs
- Summary
- Abstract
- Description
- Claims
- Application Information
AI Technical Summary
Problems solved by technology
Method used
Image
Examples
Embodiment 1
[0047] The FCC gasoline 1 is pre-separated in the fractionation tower of the catalytic cracking unit to obtain light fractions and heavy fractions. The separation temperature of the light fractions and the heavy fractions is 125°C; the light fractions undergo alkali-free deodorization, and then enter the hydrogenation pre-fractionation tower for processing After separation, the separation temperature of light gasoline and medium gasoline obtained is 65°C.
[0048] The conditions for alkali-free deodorization are: reactor operating pressure 0.6MPa, reaction temperature 35°C, feed space velocity 0.9h -1 , The air / feed volume ratio is 0.7. The pre-hydrogenation reaction conditions of the fractions in catalytic gasoline are: hydrogen partial pressure 1.8MPa and volumetric space velocity 3.8 h -1 The reaction temperature is 178℃; the hydrodesulfurization reaction conditions of the distillate in catalytic gasoline are: hydrogen partial pressure 1.6MPa, volumetric space velocity 3.0h -1 ...
Embodiment 2
[0051] The FCC gasoline 2 is pre-separated in the fractionation tower of the catalytic cracking unit to obtain light fractions and heavy fractions; the separation temperature of the light fractions and heavy fractions is 120°C; the light fractions undergo alkali-free deodorization, and then enter the hydrogenation pre-fractionation tower for processing The separation temperature of the obtained light gasoline and medium gasoline is 70°C.
[0052] The conditions for alkali-free deodorization are: reactor operating pressure 0.5MPa, reaction temperature 45°C, and feed space velocity 0.8 h -1 , The air / feed volume ratio is 0.6. The pre-hydrogenation reaction conditions of the fractions in catalytic gasoline are: hydrogen partial pressure 2.0MPa, volumetric space velocity 3.8h -1 The reaction temperature is 183℃; the hydrodesulfurization reaction conditions of the distillate in catalytic gasoline are: hydrogen partial pressure 1.8MPa, volumetric space velocity 3.2 h -1 , Reaction tempe...
Embodiment 3
[0055] The FCC gasoline 3 is pre-separated in the fractionation tower of the catalytic cracking unit to obtain light fractions and heavy fractions; the separation temperature of the light fractions and heavy fractions is 130°C; the light fractions undergo alkali-free deodorization, and then enter the catalytic gasoline fractions for hydrogenation The pre-fractionation tower performs separation, and the separation temperature of light gasoline and medium gasoline obtained is 68°C.
[0056] The conditions for alkali-free deodorization are: reactor operating pressure 0.5MPa, reaction temperature 40℃, and feed space velocity 1.1 h -1 , The air / feed volume ratio is 1.0. The pre-hydrogenation reaction conditions of the distillate in catalytic gasoline are: hydrogen partial pressure 1.8MPa, volumetric space velocity 4.2 h -1 The reaction temperature is 180℃; the hydrodesulfurization reaction conditions of the distillate in catalytic gasoline are: hydrogen partial pressure 1.6MPa, volumet...
PUM
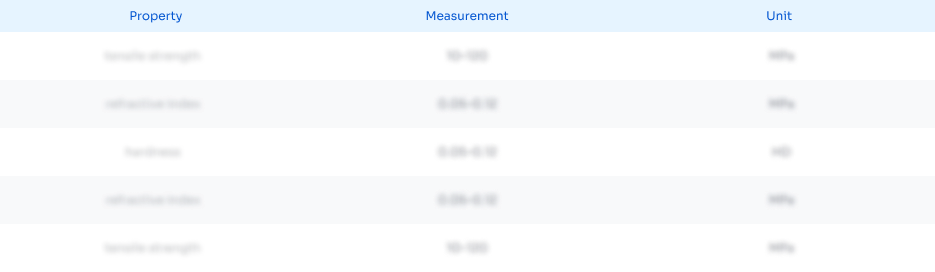
Abstract
Description
Claims
Application Information

- R&D
- Intellectual Property
- Life Sciences
- Materials
- Tech Scout
- Unparalleled Data Quality
- Higher Quality Content
- 60% Fewer Hallucinations
Browse by: Latest US Patents, China's latest patents, Technical Efficacy Thesaurus, Application Domain, Technology Topic, Popular Technical Reports.
© 2025 PatSnap. All rights reserved.Legal|Privacy policy|Modern Slavery Act Transparency Statement|Sitemap|About US| Contact US: help@patsnap.com