Method for preparing rehydration bacterial cellulose membrane by utilizing vegetable protein and hydrolysate thereof
A technology of bacterial cellulose membrane and bacterial cellulose is applied in the field of preparing rehydration bacterial cellulose membrane, which can solve the problem of not finding rehydration bacterial cellulose membrane, and achieve the effect of excellent rehydration performance and high affinity
- Summary
- Abstract
- Description
- Claims
- Application Information
AI Technical Summary
Problems solved by technology
Method used
Examples
Embodiment 1
[0021] (1) Soak 15g of the cellulose gel film that has been removed from the bacteria and residual culture medium in the dissolved 10% soybean protein hydrolyzate, soak the front side for 20 minutes, and the reverse side for 20 minutes. After soaking, the bacterial cellulose wet film weighs 22.6039 g.
[0022] (2) Dry the soaked cellulose film in an oven at 105°C for 4 hours to obtain a rehydrated bacterial cellulose film with a dry weight of 1.2518g. Put the cellulose film back into distilled water for 1 hour to make it swell. After rehydration, the weight of the cellulose wet film is 12.33g. After rehydration, the water content of the cellulose film reaches 89.85%. Compared with the wet film before drying, the rehydration rate It is 51.88%.
[0023] The formula for calculating the rehydration rate is as follows:
[0024] Rehydration rate = (wet weight after rehydration - dry weight) / (wet weight of original film - dry weight)
[0025] Blank test: Soak 15g of the cellulos...
Embodiment 2
[0027] (1) Soak 15g of the cellulose gel film that has removed bacteria and residual culture medium in 0.5% wheat protein solution that has been dissolved, soak the front side for 40 minutes, and the reverse side for 40 minutes. The wet weight of the bacterial cellulose film after soaking is 20.2089 g;
[0028] (2) Dry the soaked cellulose film in an oven at 105°C for 5 hours to obtain a rehydratable bacterial cellulose film with a dry weight of 0.437 g. Put the cellulose film back into distilled water for 1 hour to make it swell, and then rehydrate it. The weight of the cellulose wet film after watering was 5.91g, and the water content of the cellulose film after rehydration reached 92.61%, which was 27.68% compared with the wet film before drying.
Embodiment 3
[0030] (1) Soak 15g of the cellulose gel film that has been removed from the bacteria and residual culture medium in the 10% soybean peptide solution that has been dissolved, soak the front side for 30 minutes, and the reverse side for 30 minutes. After soaking, the bacterial cellulose wet film weighs 18.1567g ;
[0031] (2) Freeze-dry the soaked cellulose membrane to obtain a rehydratable bacterial cellulose membrane with a dry weight of 1.2068g. Put the cellulose membrane back into distilled water for 1 hour to make it swell. After rehydration, the cellulose wet membrane The weight is 12.253g, and the moisture content of the cellulose membrane after rehydration reaches 90.15%, which is 65.17% compared with the wet membrane before drying.
PUM
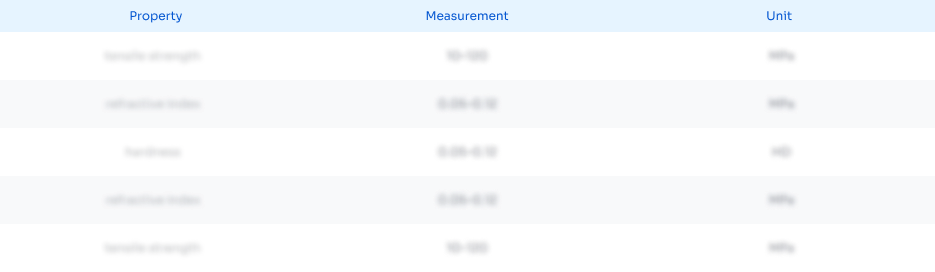
Abstract
Description
Claims
Application Information

- R&D
- Intellectual Property
- Life Sciences
- Materials
- Tech Scout
- Unparalleled Data Quality
- Higher Quality Content
- 60% Fewer Hallucinations
Browse by: Latest US Patents, China's latest patents, Technical Efficacy Thesaurus, Application Domain, Technology Topic, Popular Technical Reports.
© 2025 PatSnap. All rights reserved.Legal|Privacy policy|Modern Slavery Act Transparency Statement|Sitemap|About US| Contact US: help@patsnap.com