Variable rigidity parallel joint snake-shaped robot mechanism
A snake-shaped robot with variable stiffness technology, applied in the field of robot research and engineering, to achieve the effects of expanding the detection range, improving frictional drive efficiency, and high body flexibility
- Summary
- Abstract
- Description
- Claims
- Application Information
AI Technical Summary
Problems solved by technology
Method used
Image
Examples
Embodiment Construction
[0035] The present invention will be further described below in conjunction with the accompanying drawings.
[0036] see figure 1 As shown, the variable stiffness parallel joint snake robot mechanism provided by the present invention is composed of a plurality of identical motion units 14 connected in series; adjacent motion units 14 are connected by a two-degree-of-freedom space parallel mechanism; Each movement unit is numbered, respectively numbered as XII, XI, X, IX, VIII, VII, VI, V, IV, III, II, I; the movement state shown in the figure is U-shaped wheel movement, XII, XI, X , IX and I, II, III, IV motion units are in contact with the ground, the variable stiffness linear drives of these motion units output a small stiffness, reflecting the damping and vibration reduction function; V, VI, VII, VIII motion units are lifted off the ground .
[0037] see figure 2 , Schematic diagram of the motion unit mechanism. The motion unit is composed of four major parts: fixed U ...
PUM
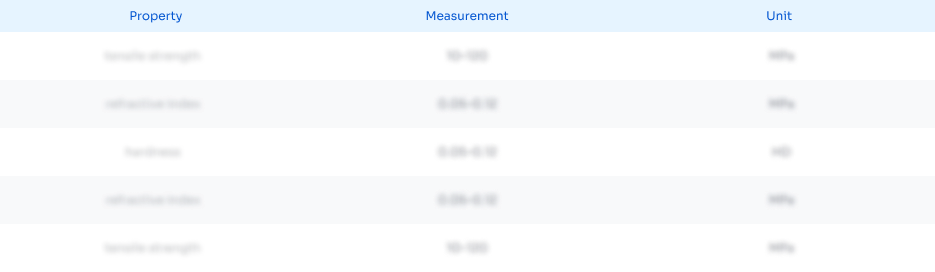
Abstract
Description
Claims
Application Information

- R&D
- Intellectual Property
- Life Sciences
- Materials
- Tech Scout
- Unparalleled Data Quality
- Higher Quality Content
- 60% Fewer Hallucinations
Browse by: Latest US Patents, China's latest patents, Technical Efficacy Thesaurus, Application Domain, Technology Topic, Popular Technical Reports.
© 2025 PatSnap. All rights reserved.Legal|Privacy policy|Modern Slavery Act Transparency Statement|Sitemap|About US| Contact US: help@patsnap.com