Radial flow two-stage disc type magneto-rheological valve
A magneto-rheological valve and disk-type technology, which is applied in the direction of fluid pressure actuators, servo motor components, mechanical equipment, etc., can solve the problems of increasing the magnetic induction intensity of the damping gap, the difficulty of the length of the effective damping gap, and the blockage of the damping gap. Wide adjustable range of differential pressure, compact internal space and stable performance
- Summary
- Abstract
- Description
- Claims
- Application Information
AI Technical Summary
Problems solved by technology
Method used
Image
Examples
Embodiment Construction
[0019] Below in conjunction with accompanying drawing and embodiment the present invention will be further described:
[0020] Such as figure 1 As shown, the present invention includes: left end cover 1, sealing ring I2, sealing ring II3, left damping disc 4, valve body 5, right damping disc 6, sealing ring III7, sealing ring IV8, right end cover 9, right positioning plate 10. Coil II11, spool 12, coil I13 and left positioning disc 14. The left end cover 1 and the valve body 5 are fixedly connected by threads, and a sealing ring I2 is arranged between the left end cover 1 and the valve body 5 . The spool 12 is in clearance fit with the valve body 5, and a sealing ring II3 and a sealing ring III7 are arranged between the spool 12 and the valve body 5. The coil I13 is wound in the winding groove I of the valve core 12 , and the coil II11 is wound in the winding groove II of the valve core 12 . When assembling, first insert the lead wires of coil I13 and coil II11 into the two...
PUM
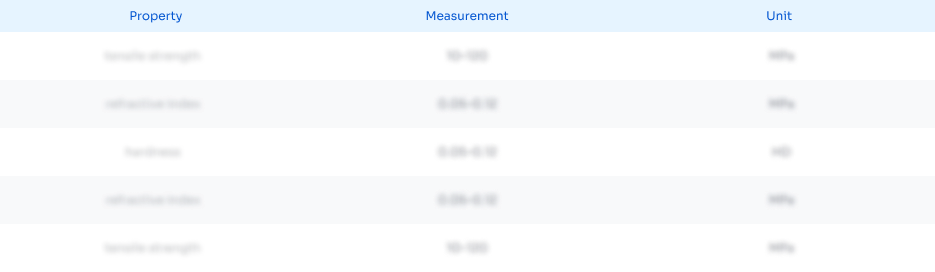
Abstract
Description
Claims
Application Information

- R&D
- Intellectual Property
- Life Sciences
- Materials
- Tech Scout
- Unparalleled Data Quality
- Higher Quality Content
- 60% Fewer Hallucinations
Browse by: Latest US Patents, China's latest patents, Technical Efficacy Thesaurus, Application Domain, Technology Topic, Popular Technical Reports.
© 2025 PatSnap. All rights reserved.Legal|Privacy policy|Modern Slavery Act Transparency Statement|Sitemap|About US| Contact US: help@patsnap.com