Method for compositely controlling micro-mechanical component by ultrasonic radiation force and moment
A technology of micro-mechanical components and ultrasonic radiation, applied in the direction of micro-structure technology, micro-structure devices, manufacturing micro-structure devices, etc., can solve the problems that micro-components cannot be captured, transported and rotated at the same time
- Summary
- Abstract
- Description
- Claims
- Application Information
AI Technical Summary
Problems solved by technology
Method used
Image
Examples
Embodiment Construction
[0017] The present invention will be further described below in conjunction with the drawings.
[0018] Such as figure 1 As shown, the ultrasonic compound manipulation system includes three components: an electronic control part, an ultrasonic transducer array and a high-speed microscopic stereo camera system. The continuous sine wave signal is generated by a multi-channel ultrasonic signal generator with programmable and adjustable parameters, and is output to the ultrasonic transducer through a high-frequency broadband linear power amplifier module. The frequency and frequency of each channel signal can be changed by the host computer system based on the PXI platform. Phase, amplitude and trigger time. The high-speed microscopic stereo camera system consists of a CCD camera, a data acquisition card and a mobile platform, which can be used to observe the movement of the micro-components and perform position calibration on the micro-components.
[0019] figure 2 It is the distrib...
PUM
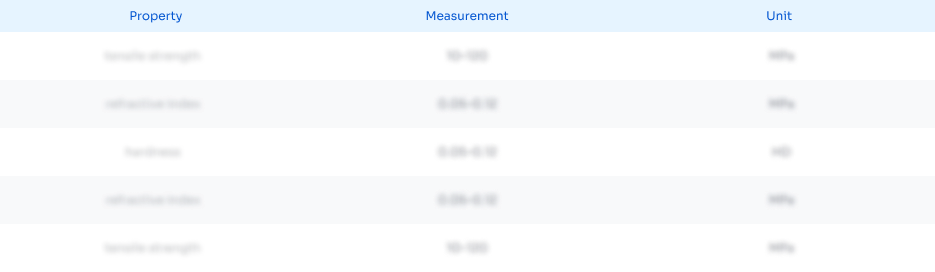
Abstract
Description
Claims
Application Information

- Generate Ideas
- Intellectual Property
- Life Sciences
- Materials
- Tech Scout
- Unparalleled Data Quality
- Higher Quality Content
- 60% Fewer Hallucinations
Browse by: Latest US Patents, China's latest patents, Technical Efficacy Thesaurus, Application Domain, Technology Topic, Popular Technical Reports.
© 2025 PatSnap. All rights reserved.Legal|Privacy policy|Modern Slavery Act Transparency Statement|Sitemap|About US| Contact US: help@patsnap.com