Fine stamping die and fine stamping method of automobile disc brake pad steel back
A technology of disc brakes and brake pads, which is applied in the field of stamping and manufacturing of auto parts, can solve the problems of increasing production equipment investment in product production costs, unfavorable multi-specification, small batch flexible production, and imperfect design of punching dies, etc., and achieves good results. Market prospects, the effect of eliminating defects and saving raw materials
- Summary
- Abstract
- Description
- Claims
- Application Information
AI Technical Summary
Problems solved by technology
Method used
Image
Examples
Embodiment Construction
[0030] The present invention relates to a fine-blanking method and a fine-blanking die for the steel back of an automobile disc brake pad. In order to make the purpose, technical solution and advantages of the present invention clearer, the present invention will be further described in detail in conjunction with the accompanying drawings.
[0031] The fine blanking method provided by the invention can use a fine blanking die on a common press to achieve the fine blanking effect, thereby improving product quality. The fine blanking method comprises the following steps:
[0032] (1) According to the area and thickness of the steel back, calculate the value range of the technological parameters of blank holder force, counter-jacking force, punching force, die edge, punching gap and die edge fillet radius, and according to Process parameters to formulate fine blanking dies;
[0033] (2) Put the plate into the mold consisting of punch, die and elastic unloading device;
[0034] ...
PUM
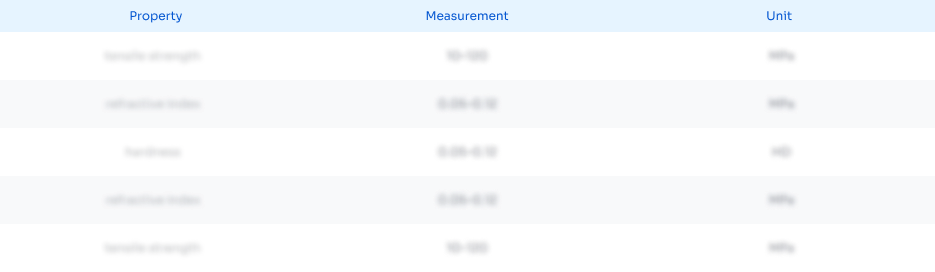
Abstract
Description
Claims
Application Information

- R&D
- Intellectual Property
- Life Sciences
- Materials
- Tech Scout
- Unparalleled Data Quality
- Higher Quality Content
- 60% Fewer Hallucinations
Browse by: Latest US Patents, China's latest patents, Technical Efficacy Thesaurus, Application Domain, Technology Topic, Popular Technical Reports.
© 2025 PatSnap. All rights reserved.Legal|Privacy policy|Modern Slavery Act Transparency Statement|Sitemap|About US| Contact US: help@patsnap.com