Chromatophilous polyurethane resin for synthetic leather and preparation method of polyurethane resin
A polyurethane resin and synthetic leather technology, applied in textiles and paper making, etc., can solve the problems of large dyeing difference, difficult dyeing of synthetic leather, different structure, etc., and achieve good wear resistance and adhesion, good breathability, and strong leather feel. Effect
- Summary
- Abstract
- Description
- Claims
- Application Information
AI Technical Summary
Problems solved by technology
Method used
Examples
Embodiment 1
[0027] Embodiment 1: polyester polyol EG1000 is 20%, polyester polyol PCL2000 is 3.5%, xylylene diisocyanate MDI is 18.5%, epoxy resin is 0.15%, triphenyl phosphite is 0.05%, Dibutyltin dilaurate is 0.02%, silicone oil is 0.01%, ethylene glycol is 0.85%, 1,4-butanediol is 3%, ethanol is 0.6%, and the rest is solvent. The solvent formula is: dimethylformamide DMF is 20%, butanone is 18%, and the rest is toluene.
[0028] The preparation method of this easily dyeable synthetic leather polyurethane resin of the present invention, the steps are as follows: earlier polyester polyol EG1000, polyester polyol PCL2000, ethylene glycol, 1,4-butanediol, epoxy resin , triphenyl phosphite and dibutyltin dilaurate were added to the reactor and dehydrated at 120°C for 1 hour; cooled to 60°C and added half of the amount of xylylene diisocyanate MDI, prepolymerized at 80~85°C for 2 hours, and the remaining Add xylene methylene diisocyanate MDI in 4~5 times, adding once every 40 minutes; after...
Embodiment 2
[0030] Embodiment 2: polyester polyol EG1000 is 15%, polyester polyol PCL2000 is 5%, xylene methylene diisocyanate MDI is 16%, epoxy resin is 0.1%, triphenyl phosphite is 0.05%, Dibutyltin dilaurate is 0.02%, silicone oil is 0.01%, ethylene glycol is 0.8%, 1,4-butanediol is 2.2%, ethanol is 0.45%, and the rest is a solvent. The solvent formula is: dimethylformamide DMF is 24%, butanone is 16%, and the rest is toluene.
[0031] The formulation of this example is especially suitable for the dyeing and discoloration treatment of shoe leather.
example 3
[0032] Example 3: 20% of polyester polyol EG1000, 5% of polyester polyol PCL2000, 20% of xylylene methylene diisocyanate MDI, 0.2% of epoxy resin, 0.05% of triphenyl phosphite, two Dibutyltin laurate is 0.02%, silicone oil is 0.01%, ethylene glycol is 1.5%, 1,4-butanediol is 3%, ethanol is 0.6%, and the rest is solvent. The solvent formula is: dimethylformamide DMF 25% for butanone, 16% for methyl ethyl ketone, and the rest for toluene.
[0033] Instructions:
[0034] 1. Put the product of the present invention on the white bass (can be embossed), and dilute the resin with ethyl acetate, butyl ester, DMF, and toluene;
[0035] 2. Take 1g of dye and 140g of water and mix well, heat up to 50°C, then add the pasted leather surface, stir or turn it over and keep it warm for about 10 minutes or take out the leather when it reaches the desired color;
[0036] 3. Rinse the leather in clean water with a slip agent for 3 minutes, then put it into a dry kneading machine and knead it d...
PUM
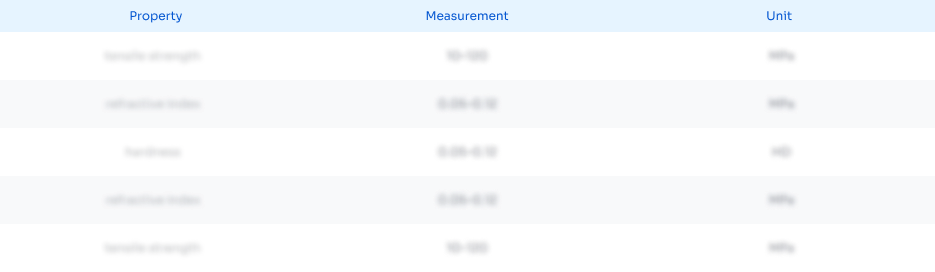
Abstract
Description
Claims
Application Information

- R&D
- Intellectual Property
- Life Sciences
- Materials
- Tech Scout
- Unparalleled Data Quality
- Higher Quality Content
- 60% Fewer Hallucinations
Browse by: Latest US Patents, China's latest patents, Technical Efficacy Thesaurus, Application Domain, Technology Topic, Popular Technical Reports.
© 2025 PatSnap. All rights reserved.Legal|Privacy policy|Modern Slavery Act Transparency Statement|Sitemap|About US| Contact US: help@patsnap.com