Method for manufacturing antistatic automotive interior non-woven fabric
A non-woven fabric and manufacturing method technology, applied in the direction of non-woven fabrics, textiles, and papermaking, can solve the problems of high manufacturing cost, limited application range, and changing the performance of fiber webs, and achieve good durability, low cost, and production process. short effect
- Summary
- Abstract
- Description
- Claims
- Application Information
AI Technical Summary
Problems solved by technology
Method used
Examples
preparation example Construction
[0020] (3) Preparation of electrospun conductive fibers
[0021] Before the air-laid fiber web enters the fiber web reinforcement process, an electrospinning device is installed, a spinneret is installed above the fiber web, and a grounded electrode plate is installed below the fiber web. The raw material of the spinning solution It is a compound of polyaniline polymer or polyaniline polymer. Connect the spinning solution to the positive pole of the high-voltage power supply, connect the grounded plate to the negative pole of the high-voltage power supply, and form a high-voltage electric field between the spinneret and the grounded plate. The spinning solution extruded from the spinneret is stretched into nanometer-scale ultrafine fibers under the action of a high-voltage electric field, and the fiber diameter is less than 1000 nanometers, which are superimposed on the fiber web to form a combined fiber web. Because the composite of polyaniline polymer and polyaniline polymer...
Embodiment 1
[0028] Airlaid Fabrication of Antistatic Needlepunched Carpet Nonwovens for Automobiles:
[0029] The method is to go through the following steps:
[0030] (1) Preparation before forming a net
[0031] The raw material is polypropylene staple fiber with a specification of 2.5D×51mm. After the raw material passes through the cotton feeding weighing machine, it is sent to the cotton blending curtain opener for opening, and the opened cotton flow enters the multi-compartment blending machine for mixing, and the mixed cotton flow is sent to the cotton opener for further processing. open loose. In the preparation stage before web formation, the fiber raw materials are loosened, and the fiber blocks are changed from large pieces to small pieces. At the same time, the fibers are evenly mixed to prepare for the fiber web formation.
[0032] (2) Fiber forming
[0033] The cotton after opening and mixing is transported by the cotton conveying fan and air-laid into the netting unit t...
Embodiment 2
[0041] Airlaid nonwovens for antistatic car roofs:
[0042] The method is to go through the following steps:
[0043] (1) Preparation before forming a net
[0044] The raw material is polypropylene staple fiber with a specification of 2.5D×51mm, and ES hot-melt staple fiber is mixed into the raw material. After the mixed raw materials pass through the cotton feeding weighing machine, they are sent to the cotton blending curtain opener for opening, and the opened cotton flow enters the multi-compartment blending machine for mixing, and the mixed cotton flow is sent to the cotton opener for re-opening. Loosen further. In the preparation stage before web formation, the fiber raw materials are loosened, and the fiber blocks are changed from large pieces to small pieces. At the same time, the fibers are evenly mixed to prepare for fiber web formation.
[0045] (2) Fiber forming
[0046] The cotton after opening and mixing is transported by the cotton conveying fan and air-laid ...
PUM
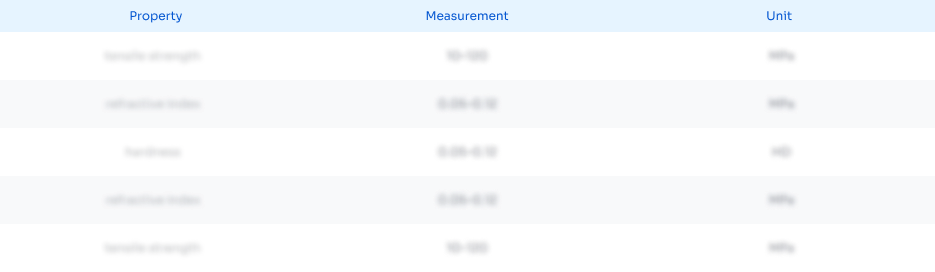
Abstract
Description
Claims
Application Information

- Generate Ideas
- Intellectual Property
- Life Sciences
- Materials
- Tech Scout
- Unparalleled Data Quality
- Higher Quality Content
- 60% Fewer Hallucinations
Browse by: Latest US Patents, China's latest patents, Technical Efficacy Thesaurus, Application Domain, Technology Topic, Popular Technical Reports.
© 2025 PatSnap. All rights reserved.Legal|Privacy policy|Modern Slavery Act Transparency Statement|Sitemap|About US| Contact US: help@patsnap.com