Coating for LDS (Laser Direct Structuring) plastic component and preparation technology thereof
A technology of plastic workpiece and preparation process, applied in the direction of polyurea/polyurethane coating, coating, device for coating liquid on the surface, etc., to achieve good adhesion, good appearance and functionality, and good matching effects
- Summary
- Abstract
- Description
- Claims
- Application Information
AI Technical Summary
Problems solved by technology
Method used
Image
Examples
Embodiment 1
[0025] This example prepares primer A1:
[0026] (1) Put 11.5 parts of ethyl acetate, 5 parts of toluene and 30 parts of ACRYLIC ZHP-189 polyurethane acrylic resin into the reaction tank and mix them at a speed of 200 rpm for 10 minutes to obtain a premix;
[0027] (2) Add 0.5 parts of BYK-358N polyether modified acrylic leveling agent, 1 part of BYK-163 wetting and dispersing agent, 2 parts of Bayer's HMP polyester adhesion promoter, and Ishihara titanium dioxide CR902 to the premix 20 parts, 20 parts of 10000 mesh talcum powder were stirred at a high speed for 35 minutes at a speed of 500 rpm, and finally 10 parts of ethyl acetate were added, and stirring was continued at a speed of 4500 rpm for 8 minutes;
[0028] (3) Grind the mixture obtained in step (2) 4 times with a blue sand machine, check that the fineness is less than 25 microns (test tool fineness plate 0~100 microns), adjust the mixture measured by KU viscometer The viscosity is 200~250GM, and the temperature con...
Embodiment 2
[0030] This example prepares primer A2:
[0031] (1) Put 10 parts of butyl ester, 12.8 parts of xylene and 45 parts of ACRYLIC ZHP-189 polyurethane acrylic resin into the reaction tank and mix them at a speed of 300 rpm for 5 minutes to obtain a premix;
[0032] (2) Add 0.2 parts of BYK-358N polyether modified acrylic leveling agent, 3 parts of BYK-163 wetting and dispersing agent, 2 parts of BYK-4510 polyester adhesion promoter, Degussa FW to the premix 4 parts of 200 carbon black, 10000 mesh talcum powder 18 high-speed stirring at 800 rpm for 30 minutes, adding 5 parts of butyl ester, and continuing to stir at 300 rpm for 10 minutes;
[0033] (3) Grind the mixture obtained in step (2) 6 times with a blue sand machine, check that the fineness is less than 25 microns (test tool fineness plate 0~100 microns), adjust the mixture measured by KU viscometer The viscosity is 200~250GM, and the temperature condition for testing the viscosity is 25±2°C; the temperature during the san...
Embodiment 3
[0035] This example prepares primer B:
[0036] (1) Put 8.8 parts of butyl acetate, 5 parts of trimethylbenzene and 50 parts of A665BA polyurethane acrylic resin into the reaction tank for mixing, and stir at a speed of 250 rpm for 8 minutes to obtain a premix;
[0037] (2) Add 0.2 parts of BYK-358N polyether modified acrylic leveling agent, 1 part of BYK-163 wetting and dispersing agent, 2 parts of Lubrizol 2063 polyester adhesion promoter, and Ishihara titanium dioxide to the premix 20 parts of CR902, 18 parts of talc powder of 10000 mesh, high-speed stirring at 1200 rpm for 30 minutes, adding 5 parts of butyl acetate, and continuing to stir at 500 rpm for 5 minutes;
[0038] (3) Grind the mixture obtained in step (2) for 3 times with a blue sand machine, check that the fineness is less than 25 microns (test tool fineness plate 0~100 microns), adjust the mixture measured by KU viscometer The viscosity is 200~250GM, and the temperature condition for testing the viscosity is ...
PUM
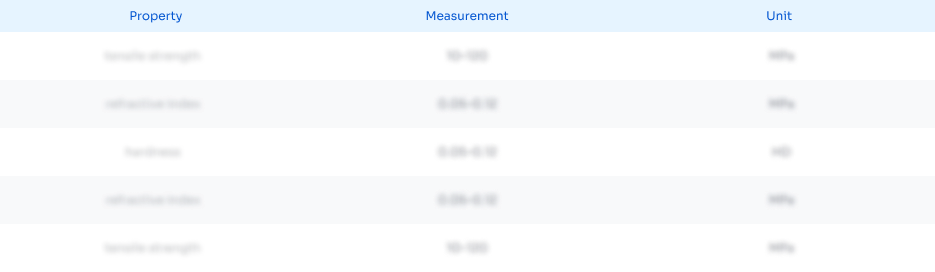
Abstract
Description
Claims
Application Information

- R&D
- Intellectual Property
- Life Sciences
- Materials
- Tech Scout
- Unparalleled Data Quality
- Higher Quality Content
- 60% Fewer Hallucinations
Browse by: Latest US Patents, China's latest patents, Technical Efficacy Thesaurus, Application Domain, Technology Topic, Popular Technical Reports.
© 2025 PatSnap. All rights reserved.Legal|Privacy policy|Modern Slavery Act Transparency Statement|Sitemap|About US| Contact US: help@patsnap.com