High flame retardant grade expandable polystyrene product and production method
A technology of expandable polystyrene and styrene, which is applied in the field of high flame-retardant expandable polystyrene products, can solve the problems that cannot meet the requirements of development, achieve high expansion ratio, good foam particle elasticity, Good flame retardant effect
- Summary
- Abstract
- Description
- Claims
- Application Information
AI Technical Summary
Problems solved by technology
Method used
Examples
example 1
[0013] Example 1: Take 100 parts by weight of styrene, 110 parts of process water, 0.05 parts of activated calcium phosphate, 0.9 parts of anhydrous sodium sulfate, 0.002 parts of sodium dodecylbenzenesulfonate, and 0.2 parts of polyethylene wax into the reactor Stir evenly, then add 0.4 parts of BPO, 0.05 parts of CP-02, 7 parts of pentane, 0.8 parts of hexabromocyclododecane, 0.5 parts of dicumyl peroxide, and heat to 90°C to start constant temperature polymerization reaction. The heating rate is controlled at 0.8°C / min, the constant temperature reaction time is 5 hours, 8 parts of pentane is added, the temperature is raised to 130°C, the heating rate is controlled at 0.2°C / min, the constant temperature reaction is 2 hours, the pressure is controlled at 0.7Mpa, and the temperature is lowered to 50°C The material can be discharged.
example 2
[0014] Example 2: Take 100 parts by weight of styrene, 130 parts of process water, 0.1 parts of activated calcium phosphate, 0.7 parts of anhydrous sodium sulfate, 0.0015 parts of sodium dodecylbenzenesulfonate, and 0.15 parts of polyethylene wax into the reactor and stir Evenly, then add 0.3 parts of BPO, 0.08 parts of CP-02, 8 parts of pentane, 0.9 parts of hexabromocyclododecane, 0.3 parts of dicumyl peroxide, and heat to 92°C to start constant temperature polymerization reaction , the heating rate is controlled at 1°C / min, the constant temperature reaction time is 5 hours, 9 parts of pentane is added, the temperature is raised to 125°C, the heating rate is controlled at 0.3°C / min, the constant temperature reaction is 3 hours, the pressure is controlled at 0.8Mpa, and the temperature is lowered to 48 ℃ can be discharged.
example 3
[0015] Example 3: Take 100 parts by weight of styrene, 120 parts of process water, 0.1 part of activated calcium phosphate, 0.7 part of anhydrous sodium sulfate, 0.001 part of sodium dodecylbenzenesulfonate, and 0.1 part of polyethylene wax into the reactor and stir Evenly, then add 0.4 parts of BPO, 0.05 parts of CP-02, 8 parts of pentane, 0.7 parts of hexabromocyclododecane, and 0.4 parts of dicumyl peroxide in sequence, and heat to 88°C to start the constant temperature polymerization reaction. The speed is controlled at 0.8°C / min, the constant temperature reaction time is 6 hours, 8 parts of pentane is added, the temperature is raised to 122°C, the heating rate is controlled at 0.4°C / min, the constant temperature reaction is 4 hours, the pressure is controlled at 0.9Mpa, and the temperature is lowered to 45°C. Can be discharged.
PUM
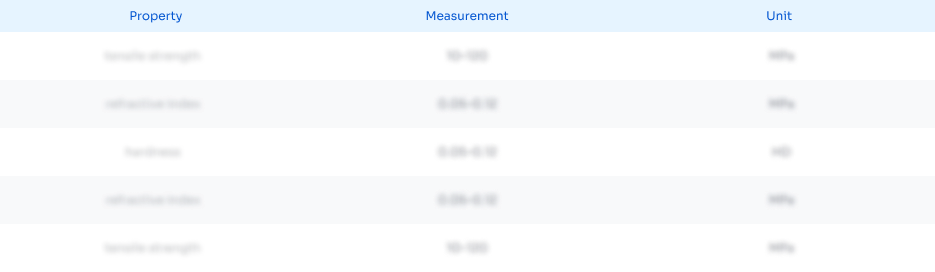
Abstract
Description
Claims
Application Information

- R&D
- Intellectual Property
- Life Sciences
- Materials
- Tech Scout
- Unparalleled Data Quality
- Higher Quality Content
- 60% Fewer Hallucinations
Browse by: Latest US Patents, China's latest patents, Technical Efficacy Thesaurus, Application Domain, Technology Topic, Popular Technical Reports.
© 2025 PatSnap. All rights reserved.Legal|Privacy policy|Modern Slavery Act Transparency Statement|Sitemap|About US| Contact US: help@patsnap.com