Control method for mechanical arm capture test on air-floating tables
A control method and a technology of a robotic arm, applied to aerospace equipment, tools, transportation and packaging, etc., can solve problems such as easy separation, insufficient friction, repeated collisions, etc., to expand the range of capture redundancy and improve self-adaptation Ability to ensure reliability
- Summary
- Abstract
- Description
- Claims
- Application Information
AI Technical Summary
Problems solved by technology
Method used
Image
Examples
Embodiment Construction
[0027] The present invention will be further introduced below in conjunction with the accompanying drawings.
[0028] The schematic diagram of the capture test of the air flotation table is as follows: figure 1 As shown, in the ground test stage, the tracking air-floating platform is used to simulate the tracking star (in-orbit controllable satellite), and the target air-floating platform is used to simulate the target star (disabled satellite); two symmetrical multi-degree-of-freedom machines are installed on the tracking air-floating platform arm. The tracking and target air bearing platform is a uniform mass cylinder with a mass of m=200Kg and a radius of the bottom surface of r=0.5m. A controller is arranged on the tracking air bearing table, and the tracking air bearing table can be moved to the target air bearing table under the control of the controller. In the process of approaching and capturing, the relative distance and relative attitude information between the tr...
PUM
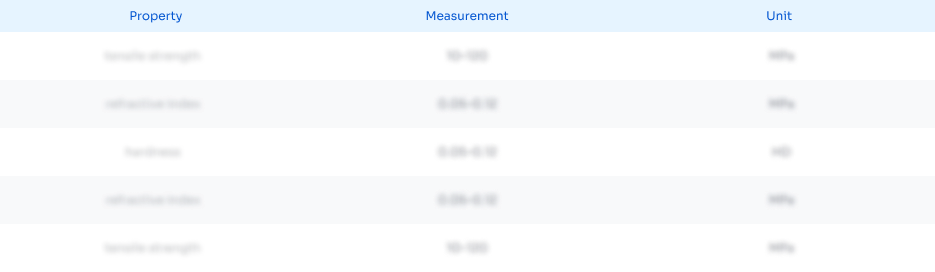
Abstract
Description
Claims
Application Information

- R&D Engineer
- R&D Manager
- IP Professional
- Industry Leading Data Capabilities
- Powerful AI technology
- Patent DNA Extraction
Browse by: Latest US Patents, China's latest patents, Technical Efficacy Thesaurus, Application Domain, Technology Topic, Popular Technical Reports.
© 2024 PatSnap. All rights reserved.Legal|Privacy policy|Modern Slavery Act Transparency Statement|Sitemap|About US| Contact US: help@patsnap.com