Production method for seamless nickel sheet with microprism array
A production method and microprism technology, which are applied in electrolytic process, electroforming and other directions, can solve the problems of large brightness attenuation, large seams, and easy cracking of nickel plates, and achieve good brightness uniformity, simple production process, and splicing accuracy. high effect
- Summary
- Abstract
- Description
- Claims
- Application Information
AI Technical Summary
Problems solved by technology
Method used
Image
Examples
Embodiment 1
[0030] Embodiment 1: The method adopted in the present invention is to arrange the unit nickel plates with microprism arrays according to requirements, and use a laser welding machine to weld the non-information side (i.e. the reverse side) of the nickel sheets, and then weld the welded nickel plates The plate is fixed on the smooth inner wall of the plastic cylinder with double-sided adhesive tape, tape, etc., and finally the seams between the unit nickel plates are eliminated by electroforming, thereby making a seamless nickel sheet with a microprism array.
specific example
[0031] A specific example is: using a seamless splicing method to make a seamless nickel sheet with a microprism junction array.
[0032] a: According to the size of the required nickel plate, cut and make four 500×500mm unit nickel plates 1 with microprism arrays;
[0033] b: Use the electroforming method to copy four nickel plates with microprism arrays, the thickness is 40 wires, and the thickness difference of each plate is controlled within 3 wires, (the thickness is controlled by the electroforming process);
[0034] Cut four unit nickel plates 1 into a square of 500×500mm by using a unidirectional low-speed wire electric discharge cutting machine, and cut the front sides of the unit nickel plate 1 to form cutting surfaces 2, and the cutting surfaces 2 and the vertical plane Form a chamfer α of 1 degree or 2 degrees or 5 degrees, and the roughness of the cutting surface 2 is controlled at Ra0.6μm or Ra0.4μm or Ra0.3μm; and the error between the unit nickel plate and the ...
PUM
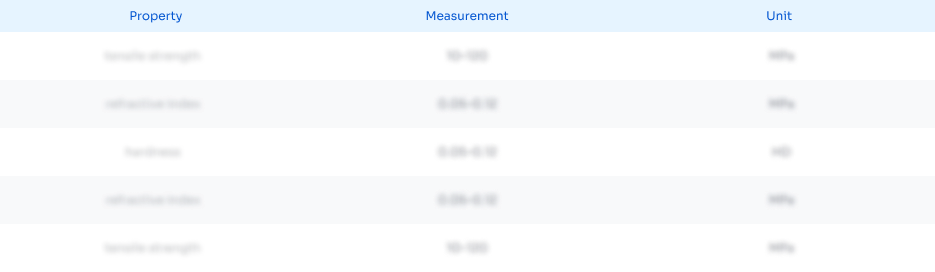
Abstract
Description
Claims
Application Information

- R&D
- Intellectual Property
- Life Sciences
- Materials
- Tech Scout
- Unparalleled Data Quality
- Higher Quality Content
- 60% Fewer Hallucinations
Browse by: Latest US Patents, China's latest patents, Technical Efficacy Thesaurus, Application Domain, Technology Topic, Popular Technical Reports.
© 2025 PatSnap. All rights reserved.Legal|Privacy policy|Modern Slavery Act Transparency Statement|Sitemap|About US| Contact US: help@patsnap.com