Loading system and method for airplane structure test
A technology of aircraft structure and loading system, which is applied in the field of aircraft testing, can solve the problems of pre-installed actuator loading, increased test cost, increased height of the loading bearing system, etc., and achieves the effect of improving loading accuracy
- Summary
- Abstract
- Description
- Claims
- Application Information
AI Technical Summary
Problems solved by technology
Method used
Image
Examples
Embodiment Construction
[0016] The present invention will be further described below in conjunction with accompanying drawing:
[0017] see figure 1 , which is a structural schematic diagram of the loading system used in the aircraft structure test of the present invention. The loading system for the aircraft structure test includes a loading bearing system, a loading beam, a fixed guide pulley, a movable pulley set, a loading connector, a first force sensor, a second force sensor, a loading actuator and ground fixed equipment, and the loading The beam is erected on the load-bearing system, the guide fixed pulley is fixed on the loading beam, the movable pulley kit is installed on the top of the loading actuator, the loading actuator is fixed on the load-bearing floor, and the loading connector surrounds the movable pulley kit and guide One end of the fixed pulley is connected with the loading beam, the other end is connected with the first force sensor, and is connected with the end of the lever sy...
PUM
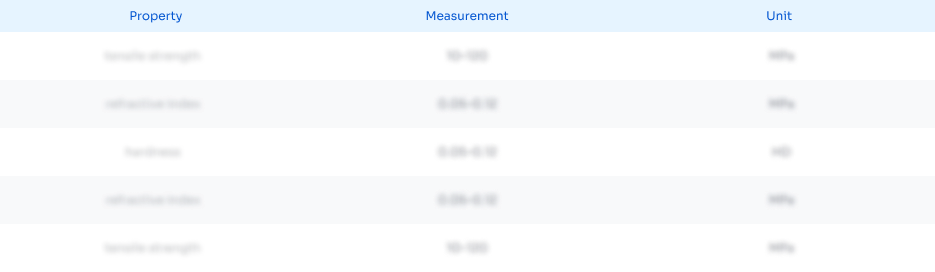
Abstract
Description
Claims
Application Information

- R&D
- Intellectual Property
- Life Sciences
- Materials
- Tech Scout
- Unparalleled Data Quality
- Higher Quality Content
- 60% Fewer Hallucinations
Browse by: Latest US Patents, China's latest patents, Technical Efficacy Thesaurus, Application Domain, Technology Topic, Popular Technical Reports.
© 2025 PatSnap. All rights reserved.Legal|Privacy policy|Modern Slavery Act Transparency Statement|Sitemap|About US| Contact US: help@patsnap.com