Piezoelectric vibratory energy harvester
A piezoelectric vibration and energy harvester technology, which is applied to generators/motors, piezoelectric effect/electrostrictive or magnetostrictive motors, electrical components, etc. , the performance of the energy harvester is degraded, etc., to achieve the effect of getting rid of the limitation of the resonance working state, improving the adaptability of the vibration source, and improving the transduction ability.
- Summary
- Abstract
- Description
- Claims
- Application Information
AI Technical Summary
Problems solved by technology
Method used
Image
Examples
Embodiment Construction
[0049] The present invention will be further described below in conjunction with the accompanying drawings and specific embodiments.
[0050] Such as figure 1 and figure 2As shown, the structure of the piezoelectric vibration energy harvester of the present invention is as follows in the order of marking: central installation structure 1, four-sided support beams 2A-2D, piezoelectric layers 3A-3D, central mass 4, and mounting arm splint 5. One end of the four support beams is clamped and installed by the installation arm of the central installation structure and the splint of the installation arm, the central mass block is installed on the square supporting plate of the central installation structure, and the piezoelectric layer is pasted on the surface of the support beam. There are lead-out electrodes on the upper and lower surfaces of the piezoelectric layer, which are used to output charges.
[0051] Such as image 3 Shown is a top view of the central mounting structur...
PUM
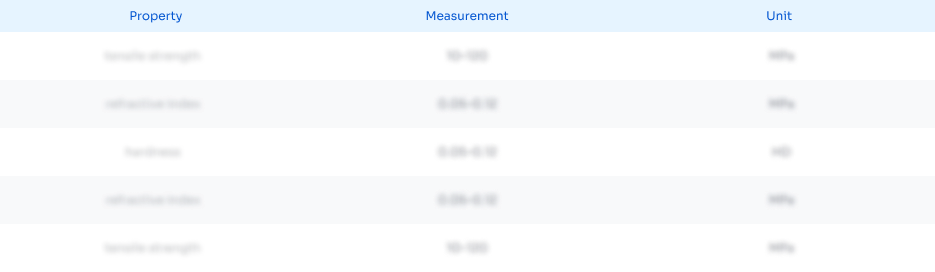
Abstract
Description
Claims
Application Information

- R&D
- Intellectual Property
- Life Sciences
- Materials
- Tech Scout
- Unparalleled Data Quality
- Higher Quality Content
- 60% Fewer Hallucinations
Browse by: Latest US Patents, China's latest patents, Technical Efficacy Thesaurus, Application Domain, Technology Topic, Popular Technical Reports.
© 2025 PatSnap. All rights reserved.Legal|Privacy policy|Modern Slavery Act Transparency Statement|Sitemap|About US| Contact US: help@patsnap.com