Method for welding eccentric circumferential seams by using electron beam scanning
A technology of electron beam scanning and eccentric ring, which is applied in the direction of electron beam welding equipment, welding equipment, metal processing equipment, etc., can solve problems such as difficult to withstand 20MPa pressure, difficult welding strength and sealing, and difficult welding of parts, so as to achieve improvement Production efficiency, avoid strong splash, reduce the effect of clamping
- Summary
- Abstract
- Description
- Claims
- Application Information
AI Technical Summary
Problems solved by technology
Method used
Image
Examples
Embodiment Construction
[0019] see Figure 1 ~ Figure 3 . In the following embodiments, only the mounting plate with an eccentric annular seam is used as the component to be welded, and this embodiment is used to further illustrate the present invention, and these embodiments are only used to illustrate the present invention without limiting the present invention. The mounting plate is mainly composed of a mounting seat 1 and a sealed oil inlet nozzle 2 to be welded, a sealed air inlet nozzle 3 , a sealed air outlet nozzle 4 , and a sealed oil outlet nozzle 5 distributed around the central axis of the installation seat 1 . Sealed oil inlet nozzle 2, sealed air inlet nozzle 3, sealed air outlet nozzle 4, and sealed oil outlet nozzle 5 are all parts to be welded with eccentric annular seams, and they are divided into electron beam welding I, II, III, and IV.
[0020] Preparation before welding. Use mechanical methods to remove the oxides on the surface of the joints of the parts, and use the organic ...
PUM
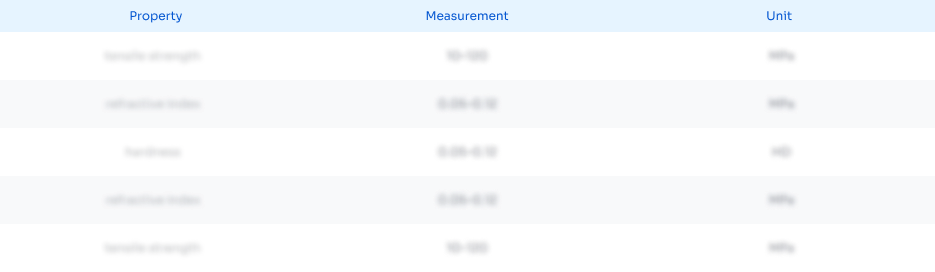
Abstract
Description
Claims
Application Information

- R&D
- Intellectual Property
- Life Sciences
- Materials
- Tech Scout
- Unparalleled Data Quality
- Higher Quality Content
- 60% Fewer Hallucinations
Browse by: Latest US Patents, China's latest patents, Technical Efficacy Thesaurus, Application Domain, Technology Topic, Popular Technical Reports.
© 2025 PatSnap. All rights reserved.Legal|Privacy policy|Modern Slavery Act Transparency Statement|Sitemap|About US| Contact US: help@patsnap.com