Flash welding shaping method for nickel-based high-temperature alloy thin-wall ring
A nickel-based high-temperature alloy and thin-walled ring technology, which is applied in welding equipment, resistance welding equipment, metal processing equipment, etc., can solve problems such as scrapped weldments, flash stop, affecting continuous welding and weld quality, and achieves good performance. Effect
- Summary
- Abstract
- Description
- Claims
- Application Information
AI Technical Summary
Problems solved by technology
Method used
Image
Examples
specific Embodiment approach
[0037] The main chemical element content (percentage by weight) of the alloy is: C content ≤ 0.08%, Cr content 17.0% ~ 21.0%, Ni content 50.0% ~ 55.0%, Co content ≤ 1.0%, Mo content 2.80% ~3.30%, Al content 0.30%~0.70%, Ti content 0.75%~1.15%, Nb content 4.75%~5.50%, B content ≤0.006%, Mg content ≤0.01%, Mn content ≤0.35 %, Si content≤0.35%, P content≤0.015%, S content≤0.015%, Cu content≤0.30%, Ca content≤0.01%, Pb content≤0.0005%, Se content≤0.0003% , The balance is Fe.
[0038] The flash welding forming process steps of the alloy thin-walled ring are as follows:
[0039] Step 1: Install the computer. Such as figure 1As shown, the GH4169 alloy D-shaped ring blank with an opening is loaded into a flash butt welding machine with a power of 1000KVA. The D-shaped ring blank is composed of a left straight edge 101, a right straight edge 102 and an arc edge 103. The side of the opening 110 corresponding to the left straight side 101 has a left end surface 111 , and the side cor...
PUM
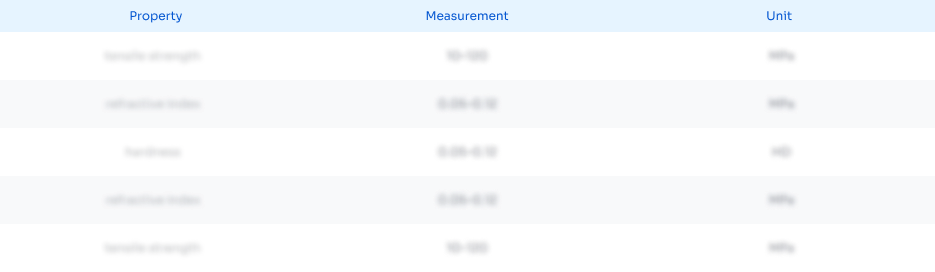
Abstract
Description
Claims
Application Information

- R&D
- Intellectual Property
- Life Sciences
- Materials
- Tech Scout
- Unparalleled Data Quality
- Higher Quality Content
- 60% Fewer Hallucinations
Browse by: Latest US Patents, China's latest patents, Technical Efficacy Thesaurus, Application Domain, Technology Topic, Popular Technical Reports.
© 2025 PatSnap. All rights reserved.Legal|Privacy policy|Modern Slavery Act Transparency Statement|Sitemap|About US| Contact US: help@patsnap.com