Radiating structure of torque motor
A motor and structure technology, applied in the field of heat dissipation structure of torque motors, can solve the problems of unfavorable heat dissipation, excessive accumulation, and influence on energy conversion efficiency in the conduction path, and achieve the effects of improving efficiency, shortening path, and increasing speed
- Summary
- Abstract
- Description
- Claims
- Application Information
AI Technical Summary
Problems solved by technology
Method used
Image
Examples
Embodiment Construction
[0022] see Figure 1 to Figure 4 As shown, the heat dissipation structure 10 of the torque motor provided in a preferred embodiment of the present invention includes an iron core 20, a cooling portion 30 made of non-magnetic material and a plurality of coils (not shown in the figure) out).
[0023] The iron core 20 is generally ring-shaped, and is a conventional motor element formed by stacking silicon steel sheets. Generally speaking, it takes a central axis as the axis, and a plurality of teeth 21 spaced apart from each other are arranged radially. Grooves 22 are formed between the teeth 21 around the central axis.
[0024] The cooling part 30 has a first end plate 31 and a second end plate 32, which are similar in shape to the end faces of the iron core 20 located at both ends of the central axis, and are fixed on the shaft of the iron core 20 with one side of the plate respectively. On the end faces of both ends, and make each of the end plates 31, 32 similar to each of ...
PUM
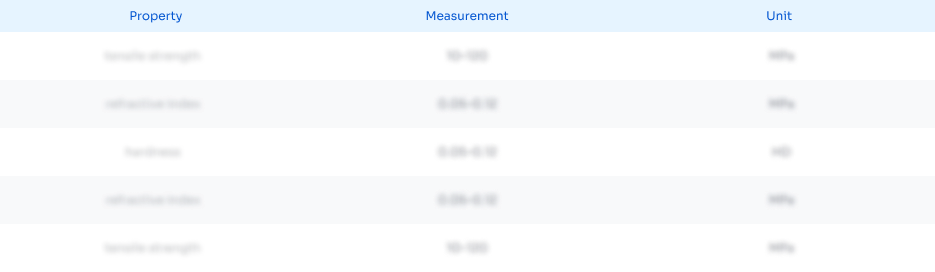
Abstract
Description
Claims
Application Information

- Generate Ideas
- Intellectual Property
- Life Sciences
- Materials
- Tech Scout
- Unparalleled Data Quality
- Higher Quality Content
- 60% Fewer Hallucinations
Browse by: Latest US Patents, China's latest patents, Technical Efficacy Thesaurus, Application Domain, Technology Topic, Popular Technical Reports.
© 2025 PatSnap. All rights reserved.Legal|Privacy policy|Modern Slavery Act Transparency Statement|Sitemap|About US| Contact US: help@patsnap.com