Forming method for stern structure of ship attached with asymmetric twisted flow control fin
A flow control and asymmetric technology, applied in the testing of machine/structural components, fluid dynamics test, hydrodynamic characteristics/hydrostatic characteristics, etc. Loss and other issues to achieve the effect of improving cavitation performance and reducing energy loss
- Summary
- Abstract
- Description
- Claims
- Application Information
AI Technical Summary
Problems solved by technology
Method used
Image
Examples
Embodiment Construction
[0014] The preferred embodiment of the present invention will now be explained in more detail, and examples of the preferred embodiment are shown in the drawings.
[0015] Since only the description of the disclosed technology is presented to illustrate the embodiments whose purpose is to describe the structure and / or function of the present invention, it should not be inferred that the scope of rights of the disclosed technology is limited by the embodiments described herein. That is, these embodiments may be modified in various ways, and therefore it should be understood that the right scope of the disclosed technology may include equivalents capable of implementing the technical spirit of the present invention. In addition, since the objectives or advantages presented in conjunction with the disclosed technology do not require specific implementations to achieve all or only one of these objectives and advantages, it should not be inferred that the scope of rights of the disclos...
PUM
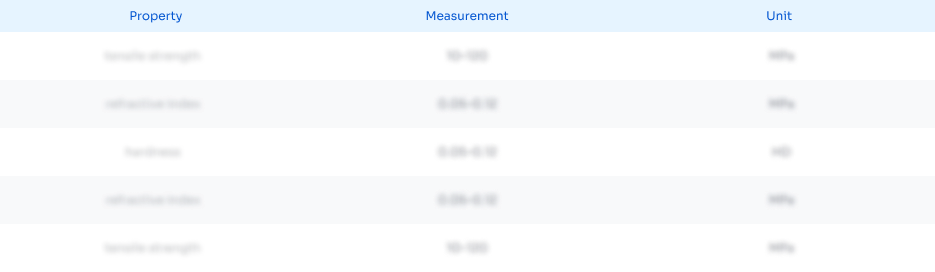
Abstract
Description
Claims
Application Information

- R&D
- Intellectual Property
- Life Sciences
- Materials
- Tech Scout
- Unparalleled Data Quality
- Higher Quality Content
- 60% Fewer Hallucinations
Browse by: Latest US Patents, China's latest patents, Technical Efficacy Thesaurus, Application Domain, Technology Topic, Popular Technical Reports.
© 2025 PatSnap. All rights reserved.Legal|Privacy policy|Modern Slavery Act Transparency Statement|Sitemap|About US| Contact US: help@patsnap.com