Production method of bamboo plywood
A production method and technology for bamboo plywood, which are applied in the joining of wooden veneers, wood treatment, wood processing appliances, etc., can solve the problems of slow drying, poor gluing performance of bamboo plywood, and reduced glue survival rate, etc. The effect of improving productivity, reducing labor intensity and ensuring product quality
- Summary
- Abstract
- Description
- Claims
- Application Information
AI Technical Summary
Problems solved by technology
Method used
Image
Examples
experiment example
[0035] A kind of bamboo plywood production method is characterized in that, comprises the following steps:
[0036] (1) Prepare a dry bamboo curtain, and control the moisture content of the bamboo curtain below 10%;
[0037] (2) Dip the bamboo curtain in glue, the glue used is phenolic resin glue, and the solid content of the glue is 25%;
[0038] (3) Under 38 degrees, use the aforementioned dehumidification room to dehumidify the soaked bamboo curtains, and dehumidify the bamboo curtains to a moisture content below 15%;
[0039] (4) Assembling the dehumidified bamboo curtains;
[0040] (5) Hot press curing.
[0041] According to the product bonding performance test method and standard requirements in the national building materials industry standard JC / T2124-2012 of "Bamboo Glue Pallets for Concrete Block (Brick) Production", the product bonding performance standard requires that the average value should be greater than or equal to 0.50MPa; Under other conditions being the...
PUM
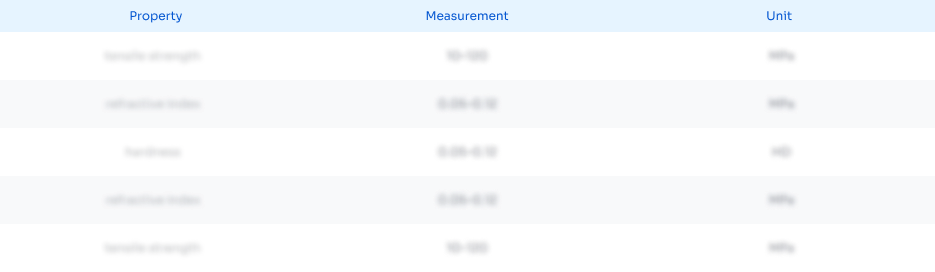
Abstract
Description
Claims
Application Information

- Generate Ideas
- Intellectual Property
- Life Sciences
- Materials
- Tech Scout
- Unparalleled Data Quality
- Higher Quality Content
- 60% Fewer Hallucinations
Browse by: Latest US Patents, China's latest patents, Technical Efficacy Thesaurus, Application Domain, Technology Topic, Popular Technical Reports.
© 2025 PatSnap. All rights reserved.Legal|Privacy policy|Modern Slavery Act Transparency Statement|Sitemap|About US| Contact US: help@patsnap.com