Detail fatigue rating (DFR) reference value determination method for folding direction connection structure stress in different phases
A technique of maximum tensile and shear stress, which is applied in the field of aviation fatigue calculation, can solve unrelated, different and equal problems, achieve simple steps, expand the calculation range, and facilitate computer programming
- Summary
- Abstract
- Description
- Claims
- Application Information
AI Technical Summary
Problems solved by technology
Method used
Image
Examples
Embodiment Construction
[0030] The present invention will be described in further detail below in conjunction with accompanying drawing, please refer to Figure 1 to Figure 3 .
[0031] Such as figure 1 As shown, it is a schematic diagram of the spanwise connection structure. The spanwise connection structure is composed of 1-left skin, 2-right skin, 3-fasteners, and 4-long truss. This structural form is widely used It is used in aircraft structures such as wing-skin butt joints and fuselage skin butt joints.
[0032] Such as figure 2 As shown in , it is a schematic diagram of the dimensions of the spanwise connection structure, and the relevant parameters used in the example are given.
[0033] Such as image 3 Shown is the fatigue stress profile, which is used in the example, and is composed of 6 load cases.
[0034] A method for determining the DFR reference value when the maximum tensile stress and the maximum shear stress of a spanwise connection structure are out of phase, comprising the ...
PUM
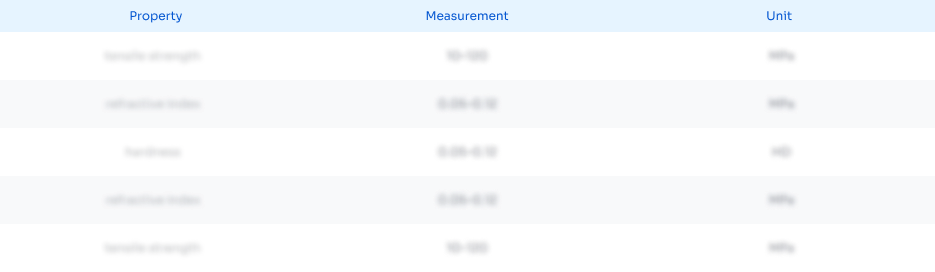
Abstract
Description
Claims
Application Information

- Generate Ideas
- Intellectual Property
- Life Sciences
- Materials
- Tech Scout
- Unparalleled Data Quality
- Higher Quality Content
- 60% Fewer Hallucinations
Browse by: Latest US Patents, China's latest patents, Technical Efficacy Thesaurus, Application Domain, Technology Topic, Popular Technical Reports.
© 2025 PatSnap. All rights reserved.Legal|Privacy policy|Modern Slavery Act Transparency Statement|Sitemap|About US| Contact US: help@patsnap.com