Setting method of hydraulic oil tank of milling equipment
A hydraulic oil tank and milling technology, applied in the hydraulic field, can solve the problems of hydraulic technology leakage, work inefficiency, heavy equipment weight, etc., and achieve the effects of improving work controllability, improving motion accuracy, and reducing labor intensity.
- Summary
- Abstract
- Description
- Claims
- Application Information
AI Technical Summary
Problems solved by technology
Method used
Examples
Embodiment Construction
[0011] The method for setting the hydraulic oil tank of the milling processing equipment described in the embodiment of the present invention, the main steps include:
[0012] (1) First, add an oil suction filter with sufficient capacity on the fuel tank to avoid too much resistance. The filter capacity of the oil filter is set to be more than twice the suction capacity of the oil pump, and an oil level indicator on the side wall of the fuel tank is set at the same height as the wall. The oil injector has a filter structure, and the inner wall of the oil tank is coated with oil-resistant paint;
[0013] (2) Separate the oil suction pipe and the oil return pipe by a certain distance, and the distance between the oil suction pipe and the bottom of the tank is greater than 3 times the pipe diameter and the distance from the tank wall is greater than 4 times the pipe diameter;
[0014] (3) The oil return pipe is inserted below the lowest oil level, the distance from the bottom of ...
PUM
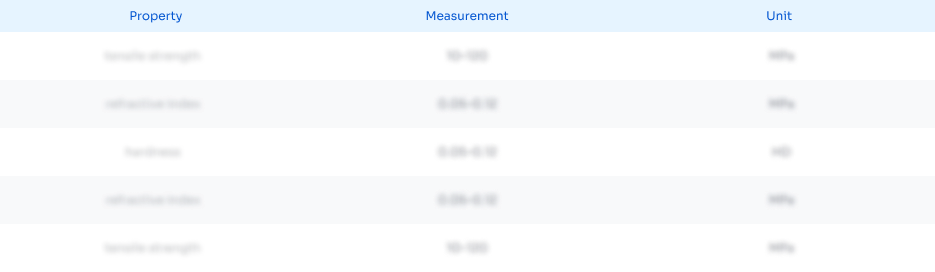
Abstract
Description
Claims
Application Information

- R&D
- Intellectual Property
- Life Sciences
- Materials
- Tech Scout
- Unparalleled Data Quality
- Higher Quality Content
- 60% Fewer Hallucinations
Browse by: Latest US Patents, China's latest patents, Technical Efficacy Thesaurus, Application Domain, Technology Topic, Popular Technical Reports.
© 2025 PatSnap. All rights reserved.Legal|Privacy policy|Modern Slavery Act Transparency Statement|Sitemap|About US| Contact US: help@patsnap.com