Coil part and manufacturing method therefor
A technology of coil components and coils, which is applied in the manufacture of motor generators, electrical components, electric components, etc. It can solve the problems of affecting the fit of pin connectors, difficulty in taking out injection molded parts, and low operating efficiency, so as to achieve reliable insulation performance and high production efficiency. Efficiency improvement, easy loading and unloading effect
- Summary
- Abstract
- Description
- Claims
- Application Information
AI Technical Summary
Problems solved by technology
Method used
Image
Examples
Embodiment Construction
[0047] The core of the present invention is to make it more convenient to disassemble the stator assembly of the coil component during injection molding, and at the same time solve the problem of fixing the pins of the coil component during injection molding, thereby improving production efficiency. Hereinafter, in conjunction with the accompanying drawings of the specification, a coil component of an electronic expansion valve and a manufacturing method thereof will be used to specifically describe the embodiments of the present invention. In the following description, the structure of the coil component and the manufacturing method will be described together.
[0048] The manufacturing method of the electronic expansion valve coil component of the present invention includes the following steps completed in sequence:
[0049] 1. Processing of various parts: including frame 10 through injection molding, pin 11, stator shell 13, electromagnetic pole plate 14 stamping, and pin protect...
PUM
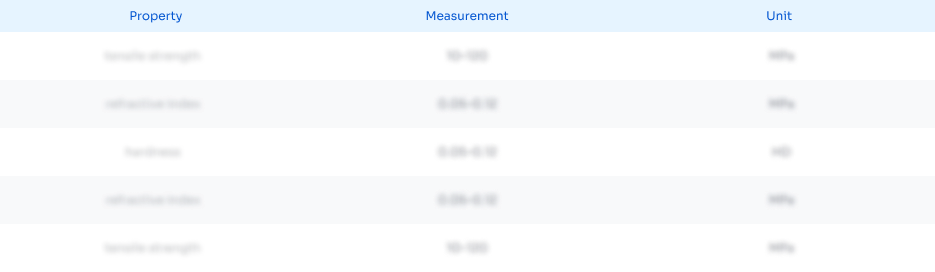
Abstract
Description
Claims
Application Information

- R&D Engineer
- R&D Manager
- IP Professional
- Industry Leading Data Capabilities
- Powerful AI technology
- Patent DNA Extraction
Browse by: Latest US Patents, China's latest patents, Technical Efficacy Thesaurus, Application Domain, Technology Topic, Popular Technical Reports.
© 2024 PatSnap. All rights reserved.Legal|Privacy policy|Modern Slavery Act Transparency Statement|Sitemap|About US| Contact US: help@patsnap.com