Boiling fluidizing roasting furnace
A fluidized roasting and boiling technology, applied in the direction of fluidized bed furnace, furnace, furnace type, etc., can solve the problems of waste of resources, reduce work efficiency, low equipment efficiency, etc., achieve faster cooling speed, improve work efficiency, and facilitate collection of effects
- Summary
- Abstract
- Description
- Claims
- Application Information
AI Technical Summary
Problems solved by technology
Method used
Image
Examples
Embodiment Construction
[0024] Embodiment 1 of the boiling type fluidized roaster of the present invention, as Figure 1-6Shown, comprise body of heater 11, the top of body of heater 11 is provided with exhaust pipe 12, and exhaust pipe 12 comprises the vertical section that is fixedly connected together with body of heater 11 and the horizontal section that is vertically fixedly connected with vertical section, so The vertical section and the horizontal section communicate with each other. In addition, the top of the vertical section is provided with a feeding hopper 13, and the outlet of the feeding hopper 13 is connected with a feed pipe, and the lower end of the feed pipe extends to the inner cavity of the furnace body 11. In the inner cavity of the furnace body 11, there is a cloth heating chamber located at the upper part and a roasting heating chamber located at the lower part. Sieve 16, in the present implementation, inverted conical sieve 16 has three layers and is arranged sequentially from...
PUM
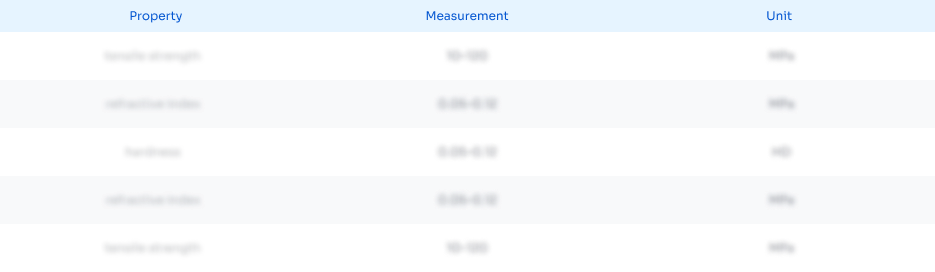
Abstract
Description
Claims
Application Information

- R&D
- Intellectual Property
- Life Sciences
- Materials
- Tech Scout
- Unparalleled Data Quality
- Higher Quality Content
- 60% Fewer Hallucinations
Browse by: Latest US Patents, China's latest patents, Technical Efficacy Thesaurus, Application Domain, Technology Topic, Popular Technical Reports.
© 2025 PatSnap. All rights reserved.Legal|Privacy policy|Modern Slavery Act Transparency Statement|Sitemap|About US| Contact US: help@patsnap.com