Rich oxygen supply process for dry-method cement rotary-kiln production
A dry-process rotary kiln and rotary kiln technology, applied in cement production, clinker production, combustion methods, etc., can solve problems such as increased investment and operating costs, high energy consumption, and difficulty in realizing flexible adjustment of oxygen-enriched combustion, and achieve reduction The effect of equipment investment and operating costs, intensification of pulverized coal combustion process, and improvement of oxygen-enriched combustion-supporting effect
- Summary
- Abstract
- Description
- Claims
- Application Information
AI Technical Summary
Problems solved by technology
Method used
Image
Examples
Embodiment 1
[0030] The VPSA oxygen-enriching device adopts multiple adsorption towers connected in parallel, and each adsorption tower is filled with dehydration adsorbent, CO removal 2 Adsorbents and molecular sieves for oxygen production. The air is treated by the oxygen-enriching device made by VPSA. Each adsorption tower alternately performs adsorption and regeneration according to the operation steps of adsorption, pressure equalization and decompression, reverse discharge, vacuuming, pressure equalization and boosting, and product gas boosting, and dehydrates in turn. , CO 2 and nitrogen, the oxygen content of the obtained oxygen-enriched gas is 32%, and the pressure is 10KPa gauge.
[0031] Such as figure 1, 25% of the oxygen-enriched gas produced by VPSA is inhaled by the fan together with the air from the coal air fan suction port of the rotary kiln and calciner, and sent as oxygen-enriched coal air to the respective multi-channel pulverized coal combustion of the rotary kiln a...
Embodiment 2
[0036] Basically the same as the technical scheme of embodiment 1, on this basis:
[0037] Such as figure 1 , the oxygen content of the oxygen-enriched gas produced by VPSA is 55%, and the pressure is 15KPa.
[0038] 45% of the oxygen-enriched gas produced by VPSA is inhaled through the fan together with the air from the coal air fan suction port of the rotary kiln and calciner. Among them, 50% of the oxygen-enriched gas is inhaled from the coal air fan inlet of the rotary kiln, and the oxygen-enriched gas with an oxygen content of 27.8% and a gauge pressure of 60 KPa is output from the fan outlet and sent to the rotary kiln as the coal air of the rotary kiln. Air duct pulverized coal burner; 50% of the oxygen-enriched gas is inhaled from the coal air fan inlet of the calciner, and the oxygen-enriched gas with an oxygen content of 27.1% and a gauge pressure of 60 KPa is output from the fan outlet as the coal air of the calciner Sent to the multi-channel pulverized coal burn...
Embodiment 3
[0041] Basically the same as the technical scheme of embodiment 1, on this basis:
[0042] Such as figure 1 , The oxygen content of the oxygen-enriched gas produced by VPSA is 75%, and the pressure is 18KPa.
[0043] 35% of the oxygen-enriched gas produced by VPSA is inhaled through the fan together with the air from the coal air fan suction port of the rotary kiln and calciner. Among them, 40% of the oxygen-enriched gas is inhaled from the coal air fan inlet of the rotary kiln, and the oxygen-enriched gas with an oxygen content of 34.8% and a gauge pressure of 120 KPa is output from the fan outlet and sent to the rotary kiln as the coal air of the rotary kiln. Air duct pulverized coal burner; 60% of the oxygen-enriched gas is inhaled from the coal air fan inlet of the calciner, and the oxygen-enriched gas with an oxygen content of 34.8% and a gauge pressure of 120 KPa is output from the outlet of the fan as the coal air of the calciner Sent to the multi-channel pulverized c...
PUM
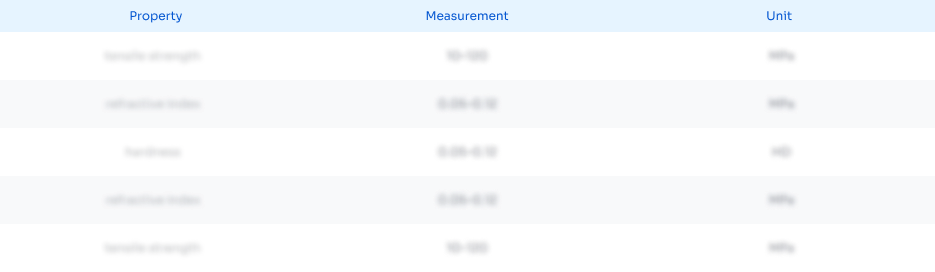
Abstract
Description
Claims
Application Information

- R&D
- Intellectual Property
- Life Sciences
- Materials
- Tech Scout
- Unparalleled Data Quality
- Higher Quality Content
- 60% Fewer Hallucinations
Browse by: Latest US Patents, China's latest patents, Technical Efficacy Thesaurus, Application Domain, Technology Topic, Popular Technical Reports.
© 2025 PatSnap. All rights reserved.Legal|Privacy policy|Modern Slavery Act Transparency Statement|Sitemap|About US| Contact US: help@patsnap.com