Automatic control system for plating thickness of hot galvanizing line
An automatic control system and coating thickness technology, applied in hot-dip plating process, coating, metal material coating process, etc., can solve the problems of long adjustment time, excessive deviation of coating thickness, poor control effect, etc., to eliminate Effects of model mismatch error, elimination of coating thickness deviation, and elimination of long-term cumulative error in the system
- Summary
- Abstract
- Description
- Claims
- Application Information
AI Technical Summary
Problems solved by technology
Method used
Image
Examples
Embodiment Construction
[0025] The specific embodiment of the present invention will be further described below in conjunction with accompanying drawing:
[0026] For a hot-dip galvanizing line in China, the distance between the thickness gauge and the air knife is 150 meters, and the running speed is 50-150 meters per minute. 6 common plating thickness specifications 80, 100, 120, 180, 220, 275g / m 2 .
[0027] 1. System configuration.
[0028] The air knife from FOEN Company in Germany, the coating thickness gauge from THERMO Company in the United States are selected, the S7-300PLC controller from SIEMENS Company is selected as the air knife controller, and the IPC427C embedded industrial PC from SIEMENS Company is selected as the industrial PC. Such as figure 1As shown, the PROFIBUS DP protocol is used for data communication between the PC and the PLC controller, the PC is used as the slave station, and the PLC controller is used as the master station. The PC side is equipped with CP5611 networ...
PUM
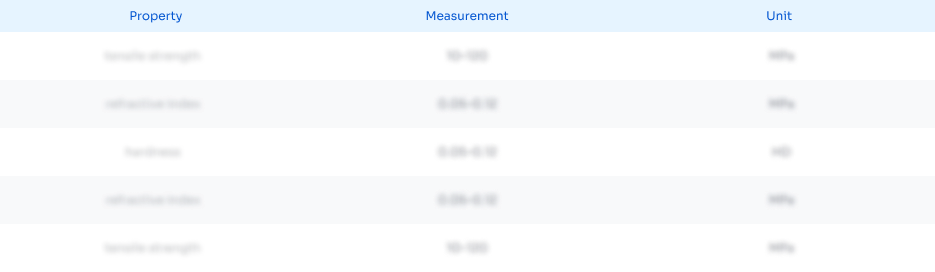
Abstract
Description
Claims
Application Information

- R&D
- Intellectual Property
- Life Sciences
- Materials
- Tech Scout
- Unparalleled Data Quality
- Higher Quality Content
- 60% Fewer Hallucinations
Browse by: Latest US Patents, China's latest patents, Technical Efficacy Thesaurus, Application Domain, Technology Topic, Popular Technical Reports.
© 2025 PatSnap. All rights reserved.Legal|Privacy policy|Modern Slavery Act Transparency Statement|Sitemap|About US| Contact US: help@patsnap.com