Polyamide-imide resin insulating varnish and method of manufacturing the same, insulated wire and coil
A technology of polyamide-imide resin and insulating coating, which is applied in the direction of plastic/resin/wax insulator, insulated cable, transformer/inductor coil/winding/connection, etc., and can solve the problems of easy partial discharge and high dielectric constant , to achieve excellent partial discharge characteristics, excellent coating operability and cost-effective effects
- Summary
- Abstract
- Description
- Claims
- Application Information
AI Technical Summary
Problems solved by technology
Method used
Image
Examples
Embodiment 1)
[0074] In the first stage of synthesis, 192 g (1.0 mol) of trimellitic anhydride as the tricarboxylic anhydride (A) of the embodiment, and 175.2 g of 4,4'-diphenylmethane diisocyanate as the diisocyanate component (B) of the embodiment (0.7 mol) and 600 g of N-methyl-2-pyrrolidone as a solvent were put into a flask, stirred at 80° C. for 2 hours, and then stirred at 100° C. for 1 hour. A flask equipped with a stirrer, a nitrogen inflow tube, and a thermometer was used for the flask. Then, the reaction solution was cooled to room temperature while maintaining the nitrogen atmosphere.
[0075] As the synthesis of the second stage, 100 g (0.5 mol) of 4,4'-diaminodiphenyl ether as the diamine component (C) of the embodiment is put into the reaction liquid, and N-methyl-2-pyrrolidone 801.6 g, stirring overnight at room temperature to obtain a polyamide-imide resin insulating coating containing an amic acid-containing compound.
Embodiment 2)
[0077] In the first stage of synthesis, 192 g (1.0 mol) of trimellitic anhydride as the tricarboxylic anhydride (A) of the embodiment, and 175.2 g of 4,4'-diphenylmethane diisocyanate as the diisocyanate component (B) of the embodiment (0.7 mol) and 600 g of N-methyl-2-pyrrolidone as a solvent were put into a flask, stirred at 80° C. for 2 hours, and then stirred at 100° C. for 1 hour. Then, the reaction solution was cooled to room temperature while maintaining the nitrogen atmosphere.
[0078] As the synthesis of the second stage, 205.1 g (0.5 moles) of 2,2-bis(4-aminophenoxyphenyl)propane, which is the diamine component (C) of the embodiment, is put into the reaction liquid, and N-methyl 1116.9 g of base-2-pyrrolidone was stirred overnight at room temperature to obtain a polyamide-imide resin insulating coating material containing an amic acid-containing compound.
Embodiment 3)
[0080]In the first stage of synthesis, 192 g (1.0 mol) of trimellitic anhydride as the tricarboxylic anhydride (A) of the embodiment, and 175.2 g of 4,4'-diphenylmethane diisocyanate as the diisocyanate component (B) of the embodiment (0.7 mol) and 600 g of N-methyl-2-pyrrolidone as a solvent were put into a flask, stirred at 80° C. for 2 hours, and then stirred at 100° C. for 1 hour. Then, the reaction solution was cooled to room temperature while maintaining the nitrogen atmosphere.
[0081] In the second stage of synthesis, 156 g (0.5 mol) of 4,4'-oxydiphthalic dianhydride as the tetracarboxylic dianhydride (D) of the embodiment, and the diamine component (C) of the embodiment were prepared. 410g (1.0 mol) of 2,2-bis(4-aminophenoxyphenyl)propane was put into the reaction solution, 2199.6g of N-methyl-2-pyrrolidone was added, and stirred overnight at room temperature to obtain The compound of polyamide-imide resin insulating coating.
PUM
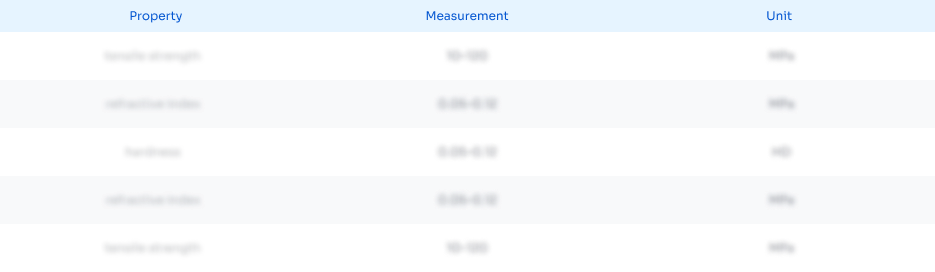
Abstract
Description
Claims
Application Information

- R&D Engineer
- R&D Manager
- IP Professional
- Industry Leading Data Capabilities
- Powerful AI technology
- Patent DNA Extraction
Browse by: Latest US Patents, China's latest patents, Technical Efficacy Thesaurus, Application Domain, Technology Topic, Popular Technical Reports.
© 2024 PatSnap. All rights reserved.Legal|Privacy policy|Modern Slavery Act Transparency Statement|Sitemap|About US| Contact US: help@patsnap.com