Preparation method of trimethyl hydroquinone
A technology of trimethylhydroquinone and trimethylbenzoquinone, which is applied in the field of preparation of trimethylhydroquinone, can solve problems such as increasing the difficulty of solvent recovery, retention of trimethylhydroquinone, and affecting product quality, so as to reduce solvent Effects of recovery loss, cycle shortening, and high product yield
- Summary
- Abstract
- Description
- Claims
- Application Information
AI Technical Summary
Problems solved by technology
Method used
Examples
Embodiment 1
[0028] Add 30 g of trimethylbenzoquinone, 250 g of ethyl acetate, and 3 g of skeleton nickel into the hydrogenation kettle. Introduce nitrogen for 2 replacements, hydrogen for 2 replacements, start stirring and heating, and when the temperature reaches 50°C, introduce hydrogen to control the reaction pressure to 1.0 MPa for hydrogenation reaction. When the pressure does not drop, the reaction basically ends. Continue the heat preservation reaction for 1 hour, and the reaction is completed. The reaction solution was heated and filtered at 50° C., and 100 g of water was added to the filtrate, and the azeotropic distillation was carried out under normal pressure to recover ethyl acetate, and the water was returned to the material. Stop after evaporating ethyl acetate, cool down to 80°C, add 0.6g of sodium hydrosulfite, keep warm at 80°C for 0.5 hours, cool down to 30°C, and filter. The wet product was dried at 80°C to obtain 28.8 g of trimethylhydroquinone with a content of 99.6...
Embodiment 2
[0030] Add 30 g of trimethylbenzoquinone, 250 g of butyl acetate, and 3 g of framework nickel into the hydrogenation kettle. Nitrogen was passed through for replacement twice, and hydrogen was replaced twice. Turn on stirring and heating, and when the temperature reaches 50° C., hydrogen gas is introduced to control the reaction pressure to 1.0 MPa to carry out the hydrogenation reaction. When the pressure does not drop, the reaction basically ends. Continue the heat preservation reaction for 1 hour, and the reaction is completed. The reaction solution was heated and filtered at 50° C., and 100 g of water was added to the filtrate, followed by azeotropic distillation under normal pressure to recover butyl acetate. The water returns to the material again, and the butyl acetate is evaporated to stop. Cool down to 80°C, add 0.6g of sodium hydroquinone, keep warm at 80°C for 0.5 hours, cool down to 30°C, filter, and dry the wet product at 80°C to obtain 28.6g of trimethylhydroqu...
Embodiment 3
[0032] Add 30 g of trimethylbenzoquinone, 250 g of isobutyl acetate, and 3 g of skeleton nickel into the hydrogenation kettle. Nitrogen was passed through for replacement twice, and hydrogen was replaced twice. Turn on stirring and heating, and when the temperature reaches 50° C., hydrogen gas is introduced to control the reaction pressure to 1.0 MPa to carry out the hydrogenation reaction. When the pressure does not drop, the reaction basically ends. Continue the heat preservation reaction for 1 hour, and the reaction is complete. The reaction liquid was heated and filtered at 50° C., and 100 g of water was added to the filtrate, followed by azeotropic distillation under normal pressure to recover isobutyl acetate. Water returns to the material again, steams the isobutyl acetate and stops, cools down to 80°C, adds 0.6g of hydrosulfite, keeps at 80°C for 0.5 hour, cools down to 30°C, filters, and dries the wet product at 80°C to obtain three Methyl hydroquinone 29.2g, the co...
PUM
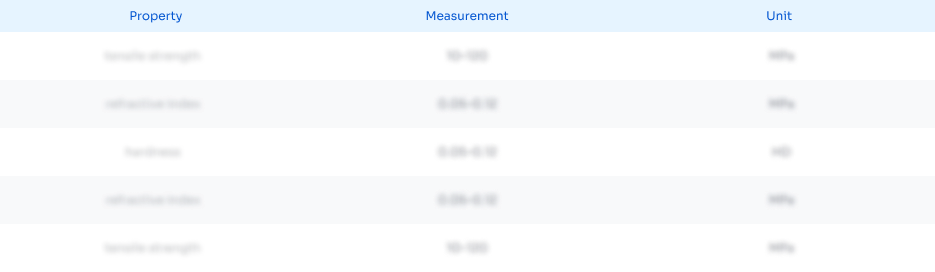
Abstract
Description
Claims
Application Information

- R&D
- Intellectual Property
- Life Sciences
- Materials
- Tech Scout
- Unparalleled Data Quality
- Higher Quality Content
- 60% Fewer Hallucinations
Browse by: Latest US Patents, China's latest patents, Technical Efficacy Thesaurus, Application Domain, Technology Topic, Popular Technical Reports.
© 2025 PatSnap. All rights reserved.Legal|Privacy policy|Modern Slavery Act Transparency Statement|Sitemap|About US| Contact US: help@patsnap.com