Veneering production process for artificial board
A production process and wood-based panel technology, applied in the field of wood processing, can solve the problems of reducing the use value, deformation, and not eliminating the stress of the veneer, so as to ensure the quality and performance, prevent deformation, and eliminate stress.
- Summary
- Abstract
- Description
- Claims
- Application Information
AI Technical Summary
Problems solved by technology
Method used
Examples
Embodiment Construction
[0015] The veneer production process of wood-based panel of the present invention comprises the following steps:
[0016] (1) First, adjust the moisture content of the base material of the wood-based panel and the veneer veneer through constant temperature and humidity conditions, so that the moisture content of the base material of the wood-based panel reaches 6-10%, and the moisture content of the veneer veneer reaches 8-12% %, and the internal moisture is evenly distributed to ensure that the moisture content of the wood-based panel base material and veneer material is not affected by the environment during the pressing process;
[0017] (2) Completely remove the dense hardened layer on the surface of the wood-based panel base material to eliminate warping, deformation or cracking of the veneer veneer due to stress imbalance or environmental changes during the veneer process;
[0018] (3) Press and paste the veneer veneer on the surface of the above wood-based panel base ma...
PUM
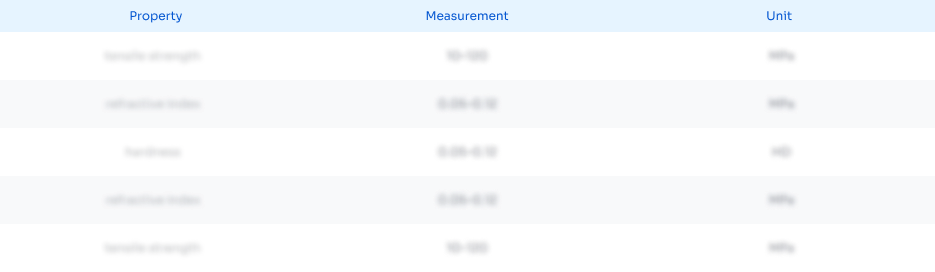
Abstract
Description
Claims
Application Information

- R&D
- Intellectual Property
- Life Sciences
- Materials
- Tech Scout
- Unparalleled Data Quality
- Higher Quality Content
- 60% Fewer Hallucinations
Browse by: Latest US Patents, China's latest patents, Technical Efficacy Thesaurus, Application Domain, Technology Topic, Popular Technical Reports.
© 2025 PatSnap. All rights reserved.Legal|Privacy policy|Modern Slavery Act Transparency Statement|Sitemap|About US| Contact US: help@patsnap.com