Double-degree-of-freedom robot wrist joint steering engine
A technology of robot wrist and degrees of freedom, applied in the field of robots, can solve the problems of large inertia and poor dynamic response of the body, and achieve the effect of compact joint structure, excellent dynamic performance and small inertia.
- Summary
- Abstract
- Description
- Claims
- Application Information
AI Technical Summary
Problems solved by technology
Method used
Image
Examples
Embodiment Construction
[0026] The present invention will be further described below in conjunction with drawings and embodiments.
[0027] figure 1 Shown is a schematic diagram of the steering gear. It is a criss-cross structure, and there is an output shaft in each of the two axis directions to provide driving force.
[0028] Such as figure 2 Shown is the assembly explosion diagram of the steering gear. The steering gear consists of top cover 1, cross fixing piece 2, Y-direction transmission shaft 3, X-direction transmission shaft 4, fixing screws 5, control circuit board 6, top cover screws 7, shell Body 8, Y-direction deceleration head 9, Y-direction angle sensor 10, Y-direction bearing bushing 11, Y-direction bearing 12, Y-direction output end cover 13, Y-direction output end cover screw 14, X-direction deceleration head 15, X-direction Angle sensor 16, X-direction bearing bushing 17, X-direction bearing 18, X-direction output end cover 19, X-direction output end cover screw 20, Y-direction ...
PUM
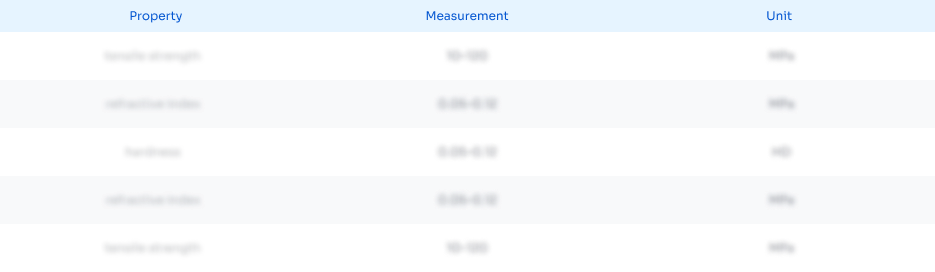
Abstract
Description
Claims
Application Information

- R&D
- Intellectual Property
- Life Sciences
- Materials
- Tech Scout
- Unparalleled Data Quality
- Higher Quality Content
- 60% Fewer Hallucinations
Browse by: Latest US Patents, China's latest patents, Technical Efficacy Thesaurus, Application Domain, Technology Topic, Popular Technical Reports.
© 2025 PatSnap. All rights reserved.Legal|Privacy policy|Modern Slavery Act Transparency Statement|Sitemap|About US| Contact US: help@patsnap.com