Apparatus and method for recycling recovery of the valuable metal by alkaline leaching
一种有价金属、回收装置的技术,应用在回收利用技术、工艺效率的提高、细胞等方向,能够解决工序费用上涨、效率低下、处理时间长等问题,达到实现装置效率性、防止气体渗漏、改善回收率的效果
- Summary
- Abstract
- Description
- Claims
- Application Information
AI Technical Summary
Problems solved by technology
Method used
Image
Examples
Embodiment 1
[0071] As a solution for the electrolytic chlorine generating cell, use 280 mL of 1 mol·L -1 Hydrochloric acid, use 280mL of 2mol L in the cathode chamber -1of NaCl solution. After the graphite electrodes respectively provided in the anode chamber and the cathode chamber were connected with electric wires, a current of 2A was applied to generate an electrochemical reaction. At this time, the pH of the cathode chamber increases as time passes while generating sodium hydroxide. When the current is applied for 450 minutes, the pH value is 13.376. At this time, the concentration of sodium hydroxide in the solution is 0.24mol L -1 .
Embodiment 2
[0073] As a solution for the electrolytic chlorine generating cell, 270 mL of 1 mol·L -1 Hydrochloric acid, use 600mL of 2mol L in the cathode chamber -1 of NaCl solution. After the graphite electrodes respectively arranged in the anode chamber and the cathode chamber are connected with electric wires, an electric current is applied to generate an electrochemical reaction. The pH of the cathode chamber increases with the generation of sodium hydroxide over time. At this time, chlorine not used in the dissolution tank was supplied to the cathode chamber to investigate the recycling rate as the chlorine recycling treatment capacity. As the supply amount of unused chlorine supplied to the cathode chamber increases, an electric current theoretically equivalent to the same generated amount of chlorine is applied to the anode chamber. The unused chlorine supply is 0.0326mol h -1 Below, showing a 100% recycling rate, the supply of unused chlorine is 0.0373mol·h -1 , showing a rec...
Embodiment 3
[0075] As a solution for the electrolytic chlorine generating cell, use 250 mL of 1 mol L in the anode chamber -1 Hydrochloric acid, use 600mL of 2mol L in the cathode chamber -1 of NaCl solution. After the graphite electrodes respectively provided in the anode chamber and the cathode chamber were connected with electric wires, a current of 2A was applied to generate chlorine gas. The generated chlorine reacts with 200ml of NaOH aqueous solution of pH 13.5 in the leaching tank to prepare OCl - The concentration is 0.9molL -1 oxidizing alkali solution. The final pH of the solution was adjusted to 13. The temperature of the prepared solution was kept at 40° C. and stirred at 400 rpm, and 1 g of ruthenium powder was charged and dissolved. The dissolution reaction was maintained for 30 minutes, and as a result, the dissolution rate reached 100%. Subsequently, the temperature of the dissolution tank was 80°C, and the injection rate of air carrier gas was 400ml·min. -1 . As a...
PUM
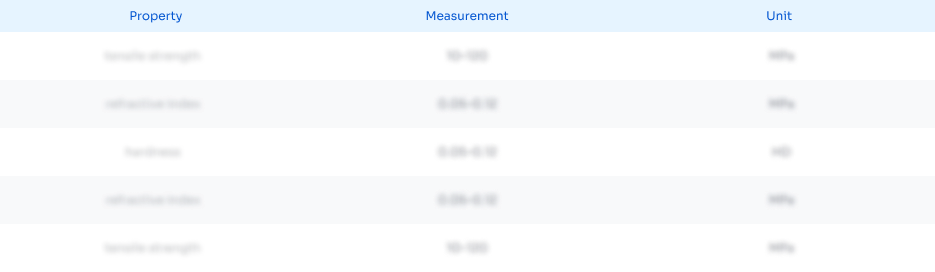
Abstract
Description
Claims
Application Information

- R&D
- Intellectual Property
- Life Sciences
- Materials
- Tech Scout
- Unparalleled Data Quality
- Higher Quality Content
- 60% Fewer Hallucinations
Browse by: Latest US Patents, China's latest patents, Technical Efficacy Thesaurus, Application Domain, Technology Topic, Popular Technical Reports.
© 2025 PatSnap. All rights reserved.Legal|Privacy policy|Modern Slavery Act Transparency Statement|Sitemap|About US| Contact US: help@patsnap.com