System and method for detecting damage of metal component nondestructively
A metal component, non-destructive testing technology, applied in the field of detection systems, can solve problems such as difficult detection, and achieve the effect of ensuring accuracy, improving reliability and accuracy
- Summary
- Abstract
- Description
- Claims
- Application Information
AI Technical Summary
Problems solved by technology
Method used
Image
Examples
no. 1 example
[0052] This embodiment provides a non-destructive detection system for metal component damage, which can perform non-destructive detection on metal components of various equipment, obtain accurate results of the damage status of metal components, and improve the reliability and accuracy of detection, such as figure 1 As shown, the system includes: a main control system, a dynamic micro-resistance monitoring system, an acoustic emission signal acquisition system, an infrared thermal signal acquisition system, and a force and displacement signal acquisition system;
[0053] Among them, the dynamic micro-resistance monitoring system is used to collect dynamic micro-resistance signals in the performance test of metal components, and to obtain micro-resistance data information after processing the micro-resistance signals;
[0054] The acoustic emission signal acquisition system collects the acoustic emission signal in the performance test of the metal component, and processes the a...
no. 2 example
[0079] The present embodiment provides a nondestructive detection method for damage to a metal component, which is a method for nondestructively detecting damage to a metal component by using the detection system provided in the first embodiment, and the method includes:
[0080] Adopt the detection system provided by the above-mentioned first embodiment;
[0081] Connecting the dynamic micro-resistance monitoring system, the acoustic emission signal acquisition system, the infrared thermal signal acquisition system and the force and displacement signal acquisition system in the system to the detected metal components respectively;
[0082] In the process of applying various mechanical property tests to the detected metal components, the dynamic micro-resistance monitoring system, the acoustic emission signal acquisition system, the infrared thermal signal acquisition system and the force and displacement data information are respectively collected through the dynamic micro-res...
PUM
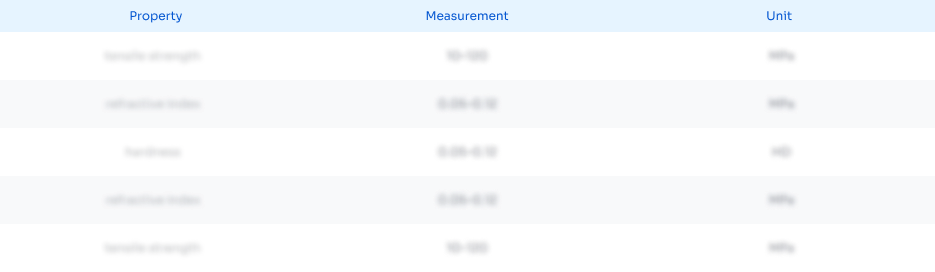
Abstract
Description
Claims
Application Information

- R&D
- Intellectual Property
- Life Sciences
- Materials
- Tech Scout
- Unparalleled Data Quality
- Higher Quality Content
- 60% Fewer Hallucinations
Browse by: Latest US Patents, China's latest patents, Technical Efficacy Thesaurus, Application Domain, Technology Topic, Popular Technical Reports.
© 2025 PatSnap. All rights reserved.Legal|Privacy policy|Modern Slavery Act Transparency Statement|Sitemap|About US| Contact US: help@patsnap.com