Assembly connecting structure and assembly connecting method of assembled concrete frame and shear wall combination
A technology for connecting structures and concrete, which is applied in the direction of walls, building components, building structures, etc., and can solve problems such as difficulty in ensuring the construction quality of joints, inconvenient construction, and too many roots
- Summary
- Abstract
- Description
- Claims
- Application Information
AI Technical Summary
Problems solved by technology
Method used
Image
Examples
Embodiment Construction
[0040] The assembly connection structure and the assembly connection method of the assembled concrete frame-shear wall of the present invention are as follows:
[0041] (1) Prefabricated or partially prefabricated columns (hereinafter referred to as prefabricated columns), prefabricated or partially prefabricated shear walls (hereinafter referred to as prefabricated walls), prefabricated or partially prefabricated beam-column joint core areas (hereinafter referred to as prefabricated nodes) and prefabricated or partially Prefabricated beams (hereinafter referred to as prefabricated beams) constitute a disassembly and assembly system of the structure. Among them, the joint core area and the beam adopt the integrated prefabrication method (hereinafter referred to as the prefabricated joint and prefabricated beam integrated component). In order to realize the mutual connection between the upper and lower columns and the vertical reinforcement between the upper and lower shear wal...
PUM
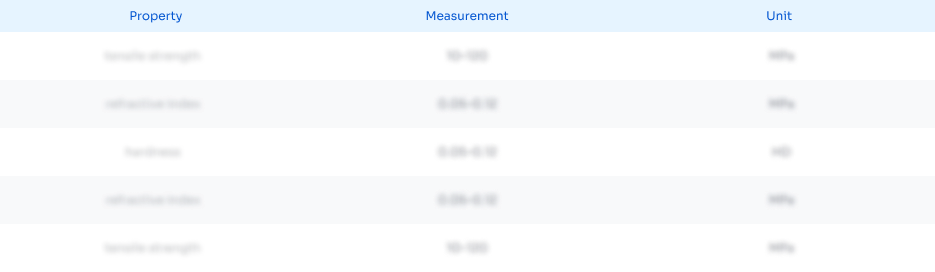
Abstract
Description
Claims
Application Information

- R&D
- Intellectual Property
- Life Sciences
- Materials
- Tech Scout
- Unparalleled Data Quality
- Higher Quality Content
- 60% Fewer Hallucinations
Browse by: Latest US Patents, China's latest patents, Technical Efficacy Thesaurus, Application Domain, Technology Topic, Popular Technical Reports.
© 2025 PatSnap. All rights reserved.Legal|Privacy policy|Modern Slavery Act Transparency Statement|Sitemap|About US| Contact US: help@patsnap.com