Manufacturing method of environment-friendly saloon car sound insulating pad
A manufacturing method and technology for sound insulation pads, which are applied to the new manufacturing of car sound insulation pads and the manufacturing field of car sound insulation pads, can solve problems such as lack of environmental protection significance, and achieve the effects of simple manufacturing process, improved sound absorption coefficient, and improved environmental performance.
- Summary
- Abstract
- Description
- Claims
- Application Information
AI Technical Summary
Problems solved by technology
Method used
Examples
Embodiment 1
[0013] (1) Preparation of forming molds: prepare forming molds according to the external dimensions of car sound insulation pads;
[0014] (2) Preparation of the base material of the sound-insulating pad: take 50% hemp palm fiber by weight, and the rest is 50% natural latex, and blend in a blending machine to obtain the base material of the sound-insulating pad;
[0015] (3) Substrate molding: heat-press the base material of the sound-insulating mat obtained in step (2) in the forming mold prepared in step (1) to obtain a semi-finished sound-insulating mat; the temperature is 100~120°C, the pressure is 7.5MPa, The molding time is 65s;
[0016] (4) Fabric lamination: Put the semi-finished sound insulation mat and fabric prepared in step (3) into the forming mold for pressing and lamination, the pressure is 7.5MPa, and the lamination time is 20s, and the finished environmentally friendly car sound insulation mat is obtained.
Embodiment 2
[0018] (1) Preparation of forming molds: prepare forming molds according to the external dimensions of car sound insulation pads;
[0019] (2) Preparation of the base material of the sound-insulating pad: take 65% hemp palm fiber by weight, and the rest is 35% natural latex, and blend in a blending machine to obtain the base material of the sound-insulating pad;
[0020] (3) Substrate molding: heat-press the base material of the sound-insulating mat obtained in step (2) in the forming mold prepared in step (1) to obtain a semi-finished sound-insulating mat; the temperature is 120~150°C, the pressure is 8MPa, The time is 50s;
[0021] (4) Fabric lamination: put the semi-finished sound insulation mat and fabric prepared in step (3) into the forming mold for pressing and lamination, the pressure is 7MPa, and the lamination time is 30s, and the finished environmentally friendly car sound insulation mat is obtained.
Embodiment 3
[0023] (1) Preparation of forming molds: prepare forming molds according to the external dimensions of car sound insulation pads;
[0024] (2) Preparation of the base material of the sound-insulating pad: take 80% hemp palm fiber by weight, and the rest is 20% natural latex, and blend in a blending machine to obtain the base material of the sound-insulating pad;
[0025] (3) Substrate molding: heat-press the base material of the sound-insulating mat obtained in step (2) in the forming mold prepared in step (1) to obtain a semi-finished sound-insulating mat; the temperature is 180~200°C, the pressure is 7MPa, The time is 70s;
[0026] (4) Fabric lamination: put the semi-finished sound insulation mat and fabric prepared in step (3) into the forming mold for pressing and lamination, the pressure is 8MPa, and the lamination time is 15s, and the finished environmentally friendly car sound insulation mat is obtained.
PUM
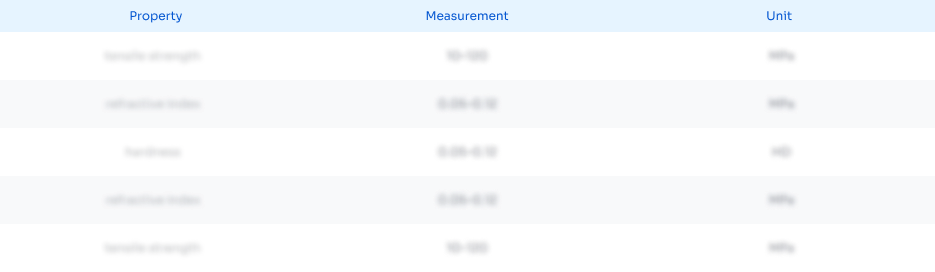
Abstract
Description
Claims
Application Information

- Generate Ideas
- Intellectual Property
- Life Sciences
- Materials
- Tech Scout
- Unparalleled Data Quality
- Higher Quality Content
- 60% Fewer Hallucinations
Browse by: Latest US Patents, China's latest patents, Technical Efficacy Thesaurus, Application Domain, Technology Topic, Popular Technical Reports.
© 2025 PatSnap. All rights reserved.Legal|Privacy policy|Modern Slavery Act Transparency Statement|Sitemap|About US| Contact US: help@patsnap.com