Structural damage location and damage assessment method based on frequency variation
A technology of damage degree and frequency change, which is applied to the analysis of solids using sound waves/ultrasonic waves/infrasonic waves, and can solve problems such as difficult measurement of degree of freedom information, incomplete structural modal parameters, and difficulty in obtaining high-order modal information.
- Summary
- Abstract
- Description
- Claims
- Application Information
AI Technical Summary
Problems solved by technology
Method used
Image
Examples
Embodiment Construction
[0078] Such as figure 1 , figure 2 Shown, the present invention adopts following steps:
[0079] The first step: establish the finite element model of the undamaged structure as the reference finite element model;
[0080] Step 2: Vibration test the damaged structure and identify the m-order modal frequency of the damaged structure ω i * ( i = 1 , . . . , m ) ;
[0081] The third step: assess the damage degree of the damaged structure;
[0082] Step 4: Determining the damage location of the damaged structure.
[0083] The specific algorithm of the above steps is deduced as follows:
[0084] 1. The reference finite element model is represented by K and M, that is, the stiffness matrix and mass matrix of the undamaged structure, and its eigenvalues are exp...
PUM
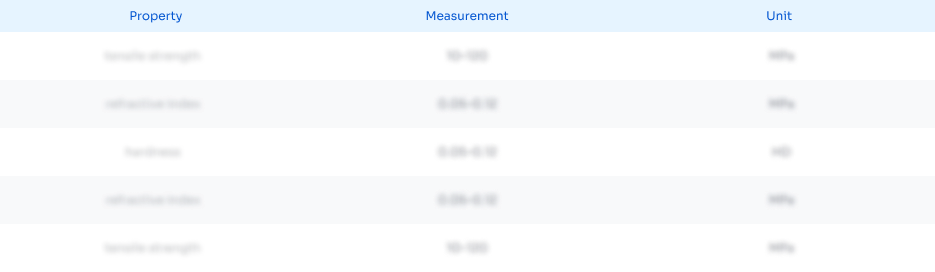
Abstract
Description
Claims
Application Information

- Generate Ideas
- Intellectual Property
- Life Sciences
- Materials
- Tech Scout
- Unparalleled Data Quality
- Higher Quality Content
- 60% Fewer Hallucinations
Browse by: Latest US Patents, China's latest patents, Technical Efficacy Thesaurus, Application Domain, Technology Topic, Popular Technical Reports.
© 2025 PatSnap. All rights reserved.Legal|Privacy policy|Modern Slavery Act Transparency Statement|Sitemap|About US| Contact US: help@patsnap.com