Method for removing sulfides in methyl tertiary butyl ether by using activated carbon
A kind of methyl tertiary butyl ether, activated carbon technology, applied in ether separation/purification, ether preparation and other directions
- Summary
- Abstract
- Description
- Claims
- Application Information
AI Technical Summary
Problems solved by technology
Method used
Image
Examples
Embodiment 1
[0016] Add commercially available powdered activated carbon into a three-necked flask containing raw material MTBE at a volume ratio of 4%, and react at room temperature for 2 hours under nitrogen protection. After the reaction stops, suck out MTBE with a syringe with a filter screen, and the refined MTBE product is analyzed by sulfur element The instrument analyzes the total sulfur content and the gas chromatography analysis type sulfur content. (See Table 1)
[0017] Table 1
[0018]
[0019]
Embodiment 2
[0021] The continuous reaction test adopts a fixed bed reactor. The reactor is equipped with 20ml granular activated carbon (20-40 mesh), and the raw material MTBE directly enters the activated carbon bed through heat exchange. The reaction temperature is controlled at 25 ° C. The volumetric space velocity of the MTBE material is 1.0h -1 , the pressure is normal pressure. After the reaction was carried out for 1 day, the refined MTBE product was analyzed by a sulfur element analyzer for total sulfur content and gas chromatographic analysis type sulfur content. (See Table 2)
[0022] Table 2
[0023]
Embodiment 3
[0024] Embodiment 3: continuous reaction test adopts fixed-bed reactor, and 20ml coconut shell spherical activated carbon (20~40 orders) is housed in the reactor, and raw material MTBE directly enters activated carbon bed layer through heat exchange, and reaction temperature is controlled at 25 ℃, The volume space velocity of MTBE material is 5.0h -1 , the pressure is normal pressure. After the reaction was carried out for 1 day, the refined MTBE product was analyzed by a sulfur element analyzer for total sulfur content and gas chromatographic analysis type sulfur content. (See Table 3)
[0025] table 3
[0026]
[0027]
PUM
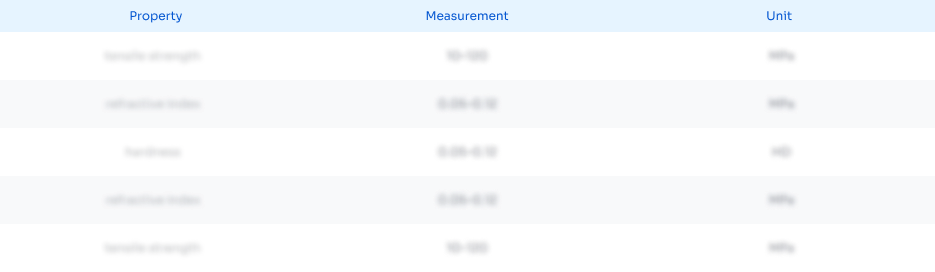
Abstract
Description
Claims
Application Information

- R&D Engineer
- R&D Manager
- IP Professional
- Industry Leading Data Capabilities
- Powerful AI technology
- Patent DNA Extraction
Browse by: Latest US Patents, China's latest patents, Technical Efficacy Thesaurus, Application Domain, Technology Topic, Popular Technical Reports.
© 2024 PatSnap. All rights reserved.Legal|Privacy policy|Modern Slavery Act Transparency Statement|Sitemap|About US| Contact US: help@patsnap.com