Optical fiber connector forming die and manufacturing method thereof
An optical fiber connector and forming mold technology, which is applied to the optical fiber connector forming mold and its production field, can solve the problems that the precision of the forming surface is difficult to meet the requirements, and the bottom edge of the forming surface is difficult to be processed in place, etc. The effect of roughness reduction and optical signal loss reduction
- Summary
- Abstract
- Description
- Claims
- Application Information
AI Technical Summary
Problems solved by technology
Method used
Image
Examples
Embodiment Construction
[0023] see Figure 1 to Figure 4 , the optical fiber connector forming mold provided by the embodiment of the present invention includes a mold core block 50 for embedding (see image 3 ) of the insert 10 and a gasket 20 that cooperates with the insert. In this embodiment, the core block 50 is a male core block, which will cooperate with a female core block (not shown) to form an optical fiber connector 60 (see Figure 4 ), that is, the mold core block 50 is only used to form the right part of the A-A line of the optical fiber connector 60 . The insert 10 and the gasket 20 participate in the molding, and only the front and rear parts of the contact surface of the output end of the optical fiber in the optical fiber connector 60 are molded, see Figure 4 Arrow B points to the square area.
[0024] Please refer to figure 1 and figure 2 , the insert 10 includes a sidewall surface 11 and two molding surfaces 12 extending from the surface 11 . The two molding surfaces 12 are...
PUM
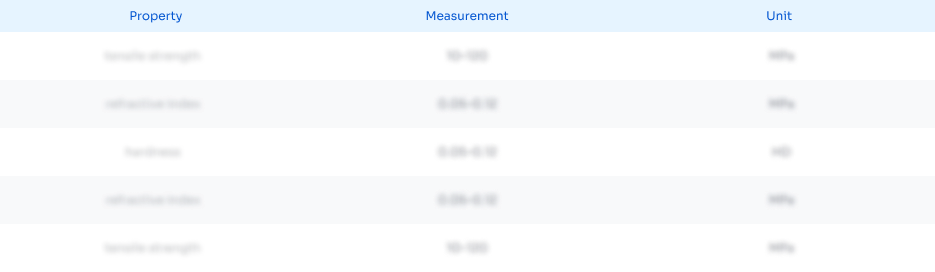
Abstract
Description
Claims
Application Information

- Generate Ideas
- Intellectual Property
- Life Sciences
- Materials
- Tech Scout
- Unparalleled Data Quality
- Higher Quality Content
- 60% Fewer Hallucinations
Browse by: Latest US Patents, China's latest patents, Technical Efficacy Thesaurus, Application Domain, Technology Topic, Popular Technical Reports.
© 2025 PatSnap. All rights reserved.Legal|Privacy policy|Modern Slavery Act Transparency Statement|Sitemap|About US| Contact US: help@patsnap.com