State monitoring device of complex electromechanical system for flow industry and method
A state monitoring device and technology in the process industry, applied in general control systems, control/regulation systems, program control, etc., can solve problems such as difficulty in monitoring variables at the same time, no unified criteria for nuclear parameter selection, and lack of equipment state characteristic information. To achieve the effect of improving fault detection ability, timely and accurate monitoring
- Summary
- Abstract
- Description
- Claims
- Application Information
AI Technical Summary
Problems solved by technology
Method used
Image
Examples
Embodiment Construction
[0049] see figure 1 , the state monitoring device of the process industry complex electromechanical system of the present invention, comprising:
[0050] Human-computer interaction module: used to realize the interaction between the user and the status monitoring system, including the input and output of system status monitoring information, calling the data acquisition module, data preprocessing module and data analysis module. It can modify and update the system fault case library, manage historical / real-time monitoring data and call the data analysis module for status monitoring.
[0051] Data acquisition module: used to extract the historical status monitoring data of the system and the real-time monitoring data generated by the DCS control system during the system operation.
[0052] Data preprocessing module: used to remove the Gaussian white noise of the monitored variable data, and standardize the collected data to remove the influence of dimension for subsequent anal...
PUM
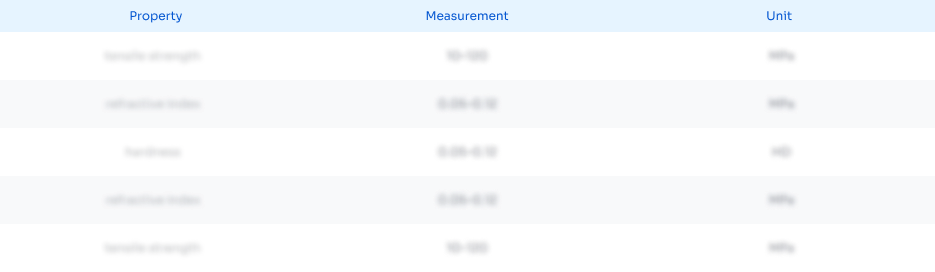
Abstract
Description
Claims
Application Information

- Generate Ideas
- Intellectual Property
- Life Sciences
- Materials
- Tech Scout
- Unparalleled Data Quality
- Higher Quality Content
- 60% Fewer Hallucinations
Browse by: Latest US Patents, China's latest patents, Technical Efficacy Thesaurus, Application Domain, Technology Topic, Popular Technical Reports.
© 2025 PatSnap. All rights reserved.Legal|Privacy policy|Modern Slavery Act Transparency Statement|Sitemap|About US| Contact US: help@patsnap.com