System for papermaking pulping
A technology of pulping and hydraulic pulping machine, applied in the field of papermaking, can solve the problems of low utilization rate of pulped fibers, difficulty in realizing continuous pulping, etc., and achieve the effect of improving fiber utilization rate
- Summary
- Abstract
- Description
- Claims
- Application Information
AI Technical Summary
Problems solved by technology
Method used
Image
Examples
Embodiment 1
[0023] A paper pulping system, such as figure 1 Shown, comprise rope winch 1, hydropulper 2, cylindrical screen 5, sediment well 3, grab hoist and impurity separator 4, rope winch 1 passes garbage rope 14 and in hydropulper 2 Junk connections.
[0024] like figure 2 As shown, the rope winching machine 1 of the present embodiment comprises a body 15, two guide wheels 13, a rope twisting wheel 12 and a rope pressing wheel 11. The surface of the rope pulley 12 is provided with a rope-grabbing protrusion group, and the rope-grabbing protrusion group is provided with a plurality of ladder-like protrusions 121, and the plurality of ladder-like protrusions 121 are mutually parallel and evenly distributed around the center line of the twisted rope wheel 12; Sheave 11 is positioned at the top of sheave sheave 12, and the two ends that press rope sheave 11 are arranged on the both sides of body 15; Garbage rope 14 enters between the twisted rope wheel 12 and the pressure rope wheel ...
Embodiment 2
[0029] A paper pulping system of this embodiment differs from Embodiment 1 in that, as image 3 As shown, the cylindrical screen 5 of this embodiment includes a motor, a casing and a screen drum. The motor is connected to the screen drum for driving. The screen drum is arranged inside the casing, and a water slurry recovery chamber is provided between the screen drum and the casing. The lower part is provided with a good pulp pipe 54 connected with the water slurry recovery chamber; the inside of the screen drum is provided with a spiral piece, and the spiral piece is arranged in a spiral shape around the central axis of the screen drum; one end of the screen drum is provided with a feed port, and the other end is There is a slag outlet. The screen drum of this embodiment is provided with helical blades to prolong the time for the slurry to pass through the cylindrical screen 5, so that the impurities and fibers of the slurry can be better separated, and the screening effect i...
PUM
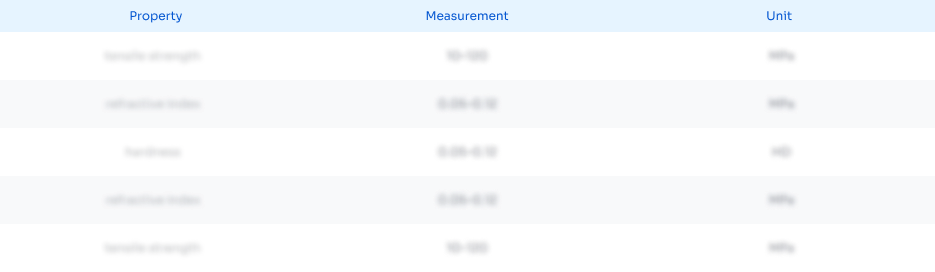
Abstract
Description
Claims
Application Information

- Generate Ideas
- Intellectual Property
- Life Sciences
- Materials
- Tech Scout
- Unparalleled Data Quality
- Higher Quality Content
- 60% Fewer Hallucinations
Browse by: Latest US Patents, China's latest patents, Technical Efficacy Thesaurus, Application Domain, Technology Topic, Popular Technical Reports.
© 2025 PatSnap. All rights reserved.Legal|Privacy policy|Modern Slavery Act Transparency Statement|Sitemap|About US| Contact US: help@patsnap.com