Preparation forming technology of aluminum foil hairline crack film
A molding process, aluminum foil technology, applied in the direction of decorative art, embossed ornaments, etc., can solve the problems of poor decorative effect, no three-dimensional effect, etc., to achieve the effect of ensuring metallic luster
- Summary
- Abstract
- Description
- Claims
- Application Information
AI Technical Summary
Problems solved by technology
Method used
Image
Examples
Embodiment Construction
[0013] refer to figure 1 As shown, the preparation and molding process of the aluminum foil hairline film in this embodiment is as follows: the aluminum foil with a thickness of 7~20um and a width of 800~1400mm passes through the force point of the hairline mold roller and the rubber roller, so that the hairline mold roller is aligned with the aluminum foil. The front side is extruded (the rubber roller squeezes the back of the aluminum foil), and the hairline mold roller is made with a concave-convex texture, so that the texture on the hairline mold roller is pressed on the aluminum foil (the front side of the aluminum foil is squeezed by the hairline abrasive roller Afterwards, a concave-convex hairline texture is produced to form an aluminum foil hairline film.
[0014] In this embodiment, the hairline mold roller is made of stainless steel, whose hardness is much greater than that of aluminum. The pressure of the force point between the hairline mold roller and the rubber...
PUM
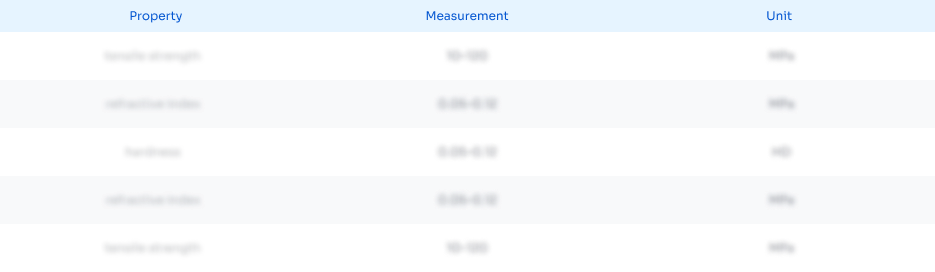
Abstract
Description
Claims
Application Information

- R&D
- Intellectual Property
- Life Sciences
- Materials
- Tech Scout
- Unparalleled Data Quality
- Higher Quality Content
- 60% Fewer Hallucinations
Browse by: Latest US Patents, China's latest patents, Technical Efficacy Thesaurus, Application Domain, Technology Topic, Popular Technical Reports.
© 2025 PatSnap. All rights reserved.Legal|Privacy policy|Modern Slavery Act Transparency Statement|Sitemap|About US| Contact US: help@patsnap.com