Pile-driving method and vibration control method
A control method and pile head technology, which can be applied in the direction of sheet pile wall, building, foundation structure engineering, etc., can solve the problems that the pile head wave node method is difficult to be practical, and achieve easy practical application, reduce the possibility of failure, and easy construction Effect
- Summary
- Abstract
- Description
- Claims
- Application Information
AI Technical Summary
Problems solved by technology
Method used
Image
Examples
Embodiment
[0064] Next, examples of the present invention will be described.
[0065] In this example, the effect obtained by applying a load to the pile head Ph was confirmed.
[0066] First, the relationship between the load applied to the pile P, the resonance frequency of the pile P, and the acceleration of the pile tip Pf during excitation (hereinafter simply referred to as tip acceleration) is confirmed.
[0067] Such as figure 2 As shown, the accelerometers A are installed at five locations along the length direction of the pile P at equal intervals from each other. Moreover, this pile P is gripped by the pile gripping apparatus 3 attached to the front-end|tip of the vibrator 2. As shown in FIG. In addition, the values obtained by dividing the sum of the mass of the pile grasping device 3 and the weight 33 by the mass of the pile P (hereinafter simply referred to as the applied load ratio) are installed on the pile grasping device 3. . And, make the power of the exciter 2 c...
PUM
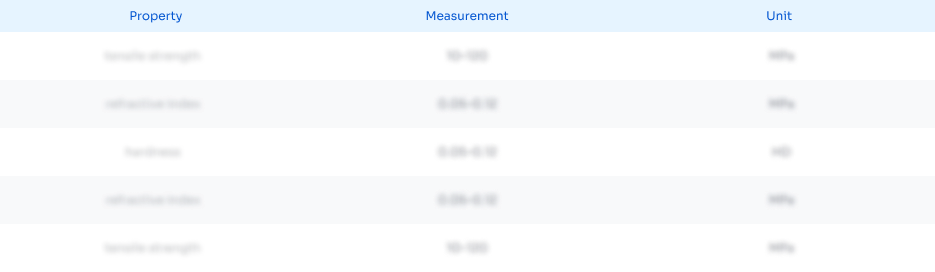
Abstract
Description
Claims
Application Information

- R&D Engineer
- R&D Manager
- IP Professional
- Industry Leading Data Capabilities
- Powerful AI technology
- Patent DNA Extraction
Browse by: Latest US Patents, China's latest patents, Technical Efficacy Thesaurus, Application Domain, Technology Topic, Popular Technical Reports.
© 2024 PatSnap. All rights reserved.Legal|Privacy policy|Modern Slavery Act Transparency Statement|Sitemap|About US| Contact US: help@patsnap.com